Digital twin has become one of the main trends or “mantras” in relation to digitalisation. It is practically a synonym of a product, something that you can buy as a commodity for a company. At CARTIF, we believe that the digital twin concept is a synonym of the Industry 4.0 paradigm, a “revolutionary” approach that has transformed the way we conceive and manage industrial processes.
The term “digital twin” was created by John Vickers of NASA in 2010, but its predecessor, the product lifecycle, was introduced by Michael Grieves in 2002. This philosophy focused on managing a product throughout its life, from creation to its disposal. In essence, the physical product generates data that feeds a virtual space, providing essential information for decision-making and optimisation of the actual object.
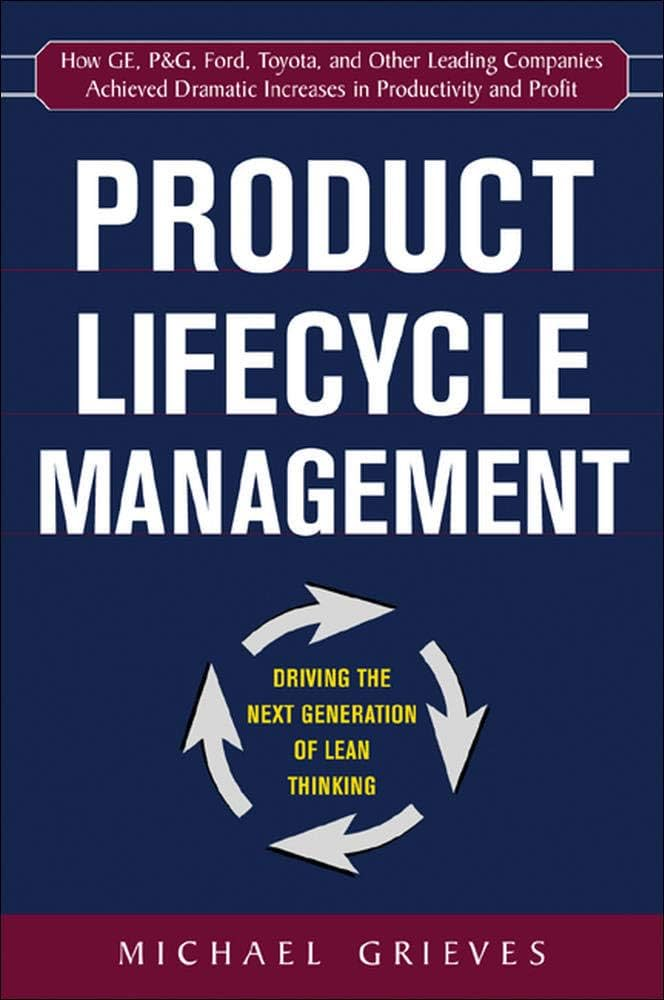
A definition of a digital twin could be “An accurate and complete digital representation of physical objects, processes or systems with real-time data and physical characteristics, behaviours and relationships”
A key questions is why do we need Digital Twins? In other words, what is their utility? These accurate, real-time digital representations offer a number of key advantages:
- Data compilation and analysis to obtain valuable information and generate knowledge, driving efficiency and informed decision-making.
- Accurate and dynamic simulation of the behaviour of physical objects, enabling virtual testing and experimentation before implementing changes, like risky investments, in the real world.
- Reducing costs and risks by minimisong risk and accelerating innovation in a wide range of sectors, from manufacturing to healthcare.
- Real-time update on a ongoing basis as new data is collected from the physical object, ensuring its validity along its lifecycle.
Like previous industrial revolutions, Industry 4.0 has transformed the way we work. This fourth revolution focuses on the interconnection of systems and processes to achieve greater efficiency throughout the value chain. The factory is no longer an isolated entity, but a node in a global production network.
To create an effective Digital Twin, at CARTIF we follow a systematic recipe of 9 steps:
- Objective definition: we identify the physical object, process or system we want to replicate and we clearly understand its purpose and objectives,
- Data compilation: we gather all relevant data from the physical object using IoT sensors, historical records or other sources of information.
- Data integration: we organise and combine the collected data in a suitable format for processing and analysis.
- Modelling and construction: we use different simulation and modelling technologies to create and accurate digital representation of the physical object.
- Validation and calibration: we verify and adjust the digital twin model using reference data and comparative tests with the real physical object.
- Real-time integration: we establish a real-time connection between the digital twin and the IoT sensors of the physical object to link real-time data.
- Analysis and simulation: we use the digital twin to make analysis, simulations and virtual tests of the physical object.
- Visualisation and shared Acces: we provide visual interfaces and shared access tools for users to interact with the digital twin.
- Maintenance and upgrade: we keep the digital twin up to date through real-time data collection, periodic calibration and incorporation of improvements and upgrades.
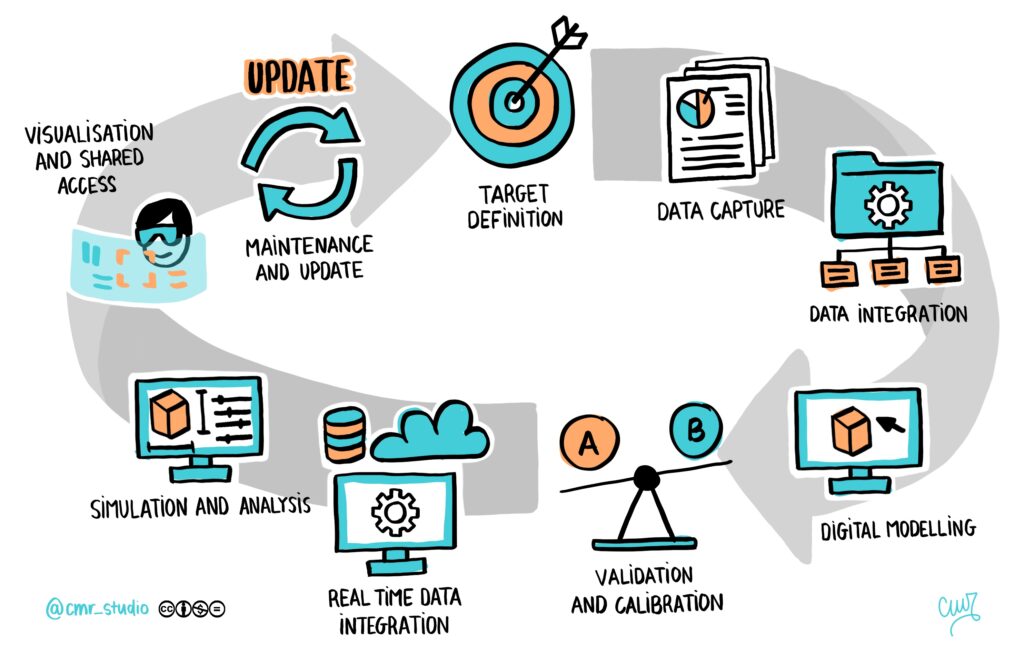
Just a previous industrial revolutions required enabling technologies, Industry 4.0 needs its own digital enablers. As we said at the beginning, we consider the digital twin a digitised form of the Industry 4.0 paradigm because digital enablers are fundamental to creating digital twins effectively. At CARTIF, we have accumulated almost 30 years of experience applying these technologies in various sectors, from industry to healthcare.
Digital enabling technologies fall into four main categories:
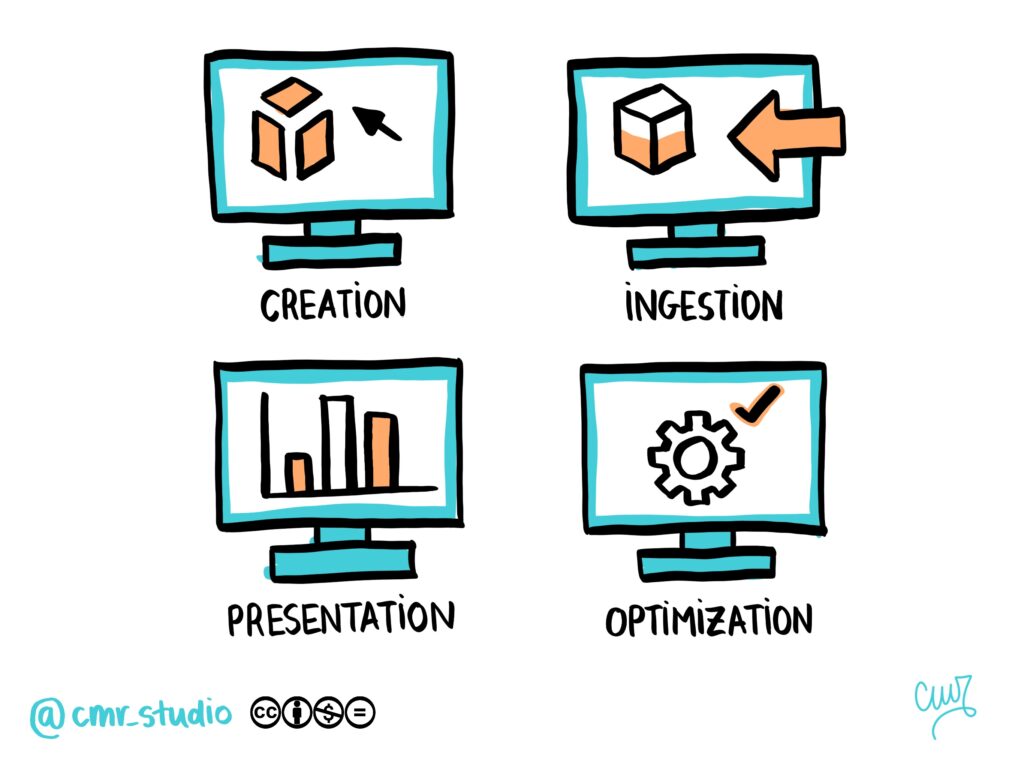
- Creation Technologies: these technologies allow the creation of Digital Twins using physical equations, data, 3D modelling or discrete events.
- Data sources: to feed digital twins, we use data integration platforms, interoperability with data sources and IoT technology.
- Optimisation: optimisation is achieved through methods such as linear or non-linear programming, simulations, AI algorithms and heuristic approaches.
- Presentation: the information generated can be presented through commercial solutions, open source tools such as Grafana or Apache superset ot even augmented reality visualisations.
Despite current progress, the challenge of keeping Digital Twins up to date remains an area of ongoing development. Automatic updating to reflect reality is a goal that requires significant investment in research and development.
In short, Digital Twins are the heart of Industry 4.0, boosting efficiency and informed decision-making. At CARTIF, we are committed to continuing to lead the way in this exciting field, helping diverse industries embrace the digital future.
- Behind the Curtain: Explainable Artificial Intelligence - 12 July 2024
- Digital Twin: Industry 4.0 in its digitised form - 9 October 2023
- Artificial Intelligence, an intelligence that needs non-artificial data - 16 December 2022