The estimation of a successful manufacturing realization is often linked to the project criteria quality, time and costs. Often it’s not possible to find optimum solutions for all criteria. For example, an exceeding quality leads to higher costs as normal. Thus, a well-elaborated project organization that focuses on a steady work flow and efficient capacity utilization is necessary to realize a manufacturing project successfully. Hence, high competence and extensive project experience are essential.
Production simulation is a very useful tool concerning the possibilities of gains in the process of production and as result, cost reduction. In order to achieve an optimum integration design vs. production, it is necessary to model not only the product but also the factories facilities and integrate them into a single simulation model. Best results are achieved when this model is linked to other optimization systems. The simulation allows finding the best workshop layout and assembly sequence according to the building strategy of the product.
In CARTIF we have experience in implementing the complexity of the production facilities in discrete simulation tools (Witness). The models allow us to ensure optimization in order to reduce production costs. We have created models for large plants (eg Renault), but also SMEs are benefiting from these advantages. For our purpose the production system can be modelled as a system where the input variables are:
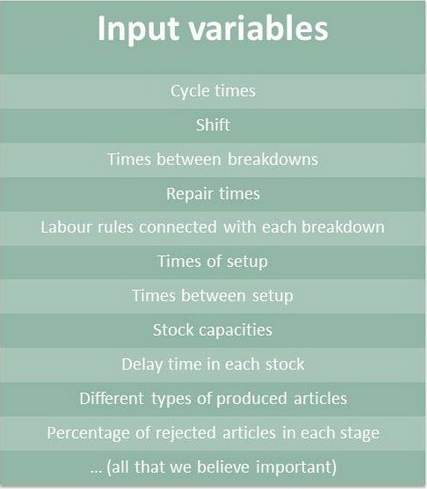
These variables can have a stochastic or a deterministic value. For instance, a timetable can be considered as a deterministic value, whereas the time between failures is a stochastic value.
The main output variables obtained from the simulation are:
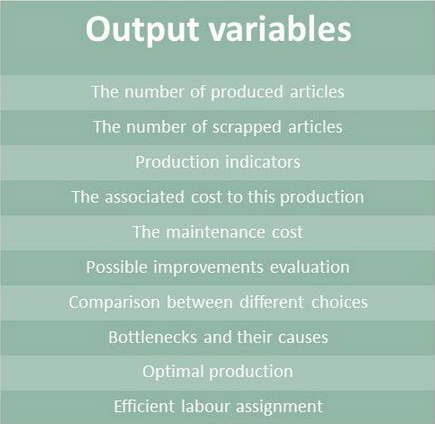
Our advice, when we think of improving our productive process, especially if it involves an investment, and we want to measure the final impact, discrete simulation is the ideal tool.
- Strategies to reduce emissions in urban bus - 24 June 2016
- Can I optimize my factory? - 22 February 2016