The biggest obstacles are not the technology barriers but the psychological and organizational barriers.
In the previous post, we explained the three steps (Reduce, Recover and Replace) through which a factory can reduce its emissions of greenhouse gases associated with its energy consumption.
Let’s suppose that Peter is a newly hired young engineer in a factory as Energy Responsible to reduce factory emissions and improve their corporate image, following the proposed steps of the REEMAIN project.
Peter, our new energy manager, logically begins with the first step: reduce, which is the easiest one be carried out, at least with respect to disconnecting the machines that are not being used. These gestures allow the factory to save energy and money at the same time. They will not usually cause tensions within the organizational structure of a factory. Using a cyclist simile, “this road is flat and with the tailwind”.
However, the next step sooner or later will analyze the different energy settings of the production systems in search of an energy settings alternative that reduces energy consumption and here, returning to cyclist similes, is where “the road becomes an uphill road”.
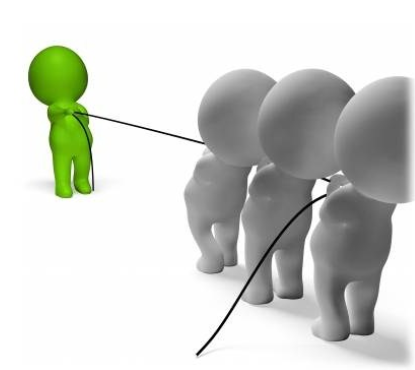
Wage incentives and bonuses for production managers are usually based mainly in the fulfillment of the planned production. This fact generates an internal pressure from up to bottom within the organization of the factory so that nothing impedes the achievement of the actual production figures. Then, once the production figures are assured, the next parameter to optimize, in terms of incentives and bonuses, is the economic cost of this production. But usually this cost, will be studied and evaluated in an aggregated or global way.
For example, casting thermal processes, usually specify a possible range of working temperatures. The minimum working temperature is that which ensures that the molten metal will not solidify prematurely under nominal operating conditions. The maximum temperature is fixed by the characteristics of the machinery itself and the product. Very occasionally, production stops due to incidentals, the molten metal is cooled slightly and this issue causes the so called “cold shut” defects, with the consequent rejection of the pieces produced, and therefore, the failure to achieve the production targets. How this problem is avoided in most cases? Opting for the easiest solution, this is, to raise the temperature of the molten metal permanently to have bigger margins against eventual stops, whether or not they finally occur.
Another practical example is the operation of the compressed air systems of the factories. Again, to avoid problems of lack of supply and the corresponding “reprimand”, maintenance chiefs set the power of the compressors to full power permanently whether or not the factory is working under full production regime.
The above examples are intended to show the fact that sometimes the energy settings of the processes are oversized with the consequent increase in energy consumption. This is because, the factory workers and managers involved in the production and maintenance perceive that do not oversizing might harm other indicators such as compliance with production planning and the total planned cost. As long as these two key performance indicators or KPIs are exclusively the only or main criteria for evaluating the performance of production workers and maintenance, there will always be internal resistance to the implementation of the changes necessary to achieve a cleaner production.
In the past, other secondary indicators, not considered important as job safety or respect for labor rights, gained importance and also became key indicators when assessing the performance of a factory. There are already companies like Google (Google Green Initiative) or IKEA (People and Planet Positive initiative) that have undertaken internal restructuring with the sole aim to reduce associated emissions even at the cost of worsening any of the economic KPIs.
In the next post, we will talk about practical examples of green manufacturing.
- Efficiency Wars (Episode VI) – The Return of Bohr - 25 July 2017
- Efficiency Wars (Episode V) – The ROI strikes back - 20 June 2017
- Efficiency Wars (Episode IV) – A new (efficiency) hope - 25 May 2017