Watch out, the game might not be worth the candle.
In my previous post, I explained how beneficial could be for a factory to disaggregate (by direct measure and not by estimations based on nominal values) the energy consumptions of the factory between the different lines, machinery and systems that compose it. Jedi jokes aside, the fact is that such energy disaggregation is an example of the well-known rule “measure to know, know to control and control to improve.” And down to a more practical approach, the availability and study of such information will allow:
- to map the energy consumptions within the factory
- to visualize, through a simple pie chart, the energy contributions of the different elements.
- to set up the priorities about what zones or machines must be modified or replaced due to their low energy efficiency.
- to compare the energy efficiency between the different lines of a factory.
- to compare the energy costs of the different products manufactured in the same production line.
- to detect inappropriate consumptions due to devices’ malfunction, or sub-optimal working protocols.
Ok, let’s suppose we have already convinced the factory managers of the convenience of measuring to improve and doing it through the disaggregation of consumption. How do we start?
The most obvious approach would be to monitor the energy consumption of each machine with its corresponding sensor or meter. For electricity consumption, the installation of a network analyser will be required in the electrical cabinet where the electrical protections associated with the equipment are located. This installation, as long as there is available space in the corresponding cabinet, usually would require stopping machines for a few minutes. In the case of machinery whose energy consumption is natural gas, things get more complicated and expensive. Here it will be necessary to saw the gas supply pipe to install the new gas meter. The safety requirements and verifications of the new weldings will require a 24-48 hours supply interruption and machinery stop.
In addition, there may be machines or equipment that require a significant consumption of compressed air or heating (or cooling) thermal energy in the form of hot (or cold) water. In these cases, the specific meters must be installed in the supply pipes of the corresponding services.
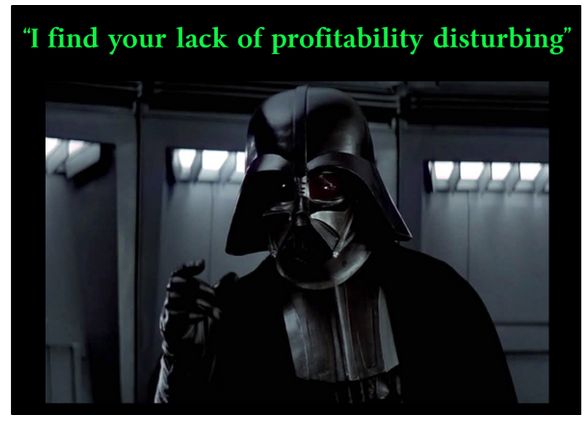
In any case, formerly, the meters used to incorporate a mechanical (or electronic) mechanism of counting and accumulation. Periodically, the assigned worker would record their readings in the corresponding logbook. The mentioned readings would be later introduced manually into the computerized cost management system. However, nowadays, this approach is obsolete since, like any manual data collection process, it is costly, inefficient and leads to multiple errors. In other words, it is not only required to install the meters, but these models must be equipped (and all industrial models comply) with a communications module that allows the measured data to be sent to a computerized database storage system. It will also be necessary to deploy a new communications network (or extend the existing one if applies) to communicate all new sensors installed with the computer system that will periodically record data on energy consumption.
This type of consumption monitoring is known as Intrusive Load Monitoring (ILM). Its main advantage is the precision of the results, but its great disadvantage is the high expenses that it entails. In factories where consumption is highly distributed among a multitude of machines, the cost of equipment and installation of an ILM system can be a great investment compared to the annual cost of energy consumption in the factory.
It should not be forgotten that the purpose of a energy disaggregation system is to help reduce energy consumption and therefore the cost associated with such consumption. Obviously, it is not possible to precisely predict the economic savings that the energy disaggregation will produce. With regards to this, it is usual to use ranges, based on previous experiences, with the most and least favourable values. No matter how wide the potential savings are, if the initial investment is unreasonably high, the corresponding Return on Investment or ROI rates will be above any acceptable threshold considered by the relevant Chief Financial Officer.
To be continued…
- Efficiency Wars (Episode VI) – The Return of Bohr - 25 July 2017
- Efficiency Wars (Episode V) – The ROI strikes back - 20 June 2017
- Efficiency Wars (Episode IV) – A new (efficiency) hope - 25 May 2017