“It is April 21, 2011. SKYNET, the Superintelligence artificial system who became self-aware 2 days earlier has launched a nuclear attack on us humans. The April 19, SKYNET system, formed by millions of computer severs all across the world, initiated a geometric self-learning process. The new artificial intelligence concluded that all of humanity would attempt to destroy it and impede its capability to continue operating”
It seems the apocalyptic vision of Artificial Intelligence depicted in Terminator science fiction movies is still far from being a reality, yet. SKYNET, our nemesis in the films, was a collection of servers, drones, military satellites, war-machines, and Terminator robots to perform a relevant task: safeguarding the world.
Today’s post is focused on a different but relevant task: manufacturing the products of the future. In our previous posts, we reviewed the Industry 4.0 key ingredients, the so-called digital enablers. The last key ingredient, Cyber Physical Systems, can be seen as the “SKYNET” of manufacturing, and we defined it as a mixture of different technologies. Now it is time to be more specific.
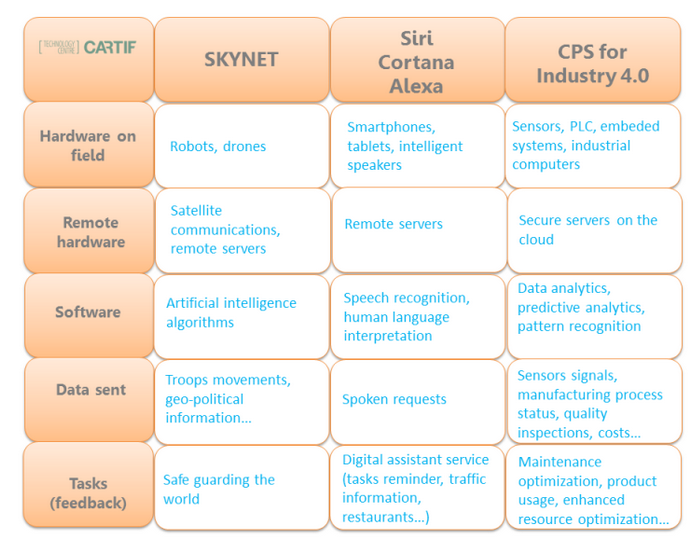
The term “cyber-physical” itself is the compound name to designate of mixture of virtual and physical systems to perform a complex task. The rapid evolution of Information and Communication Technologies (ICT) is enabling the development of services no longer contained into the shells of the devices we buy. Take for example, digital personal assistants like Siri from Apple, Alexa from Amazon or Cortana from Microsoft. These systems provide us help with everyday tasks but are not mere programs inside our smartphones. They are a mixture of hardware devices (our phones and internet servers) that take signals (our voice) and communicates with software in the cloud that makes the appropriate processing and answers after some milliseconds with an appropriate and in-context answer. The algorithms integrated into the servers are able to process the speech using sophisticated machine learning algorithms and create the appropriate answer. The combination of user phones, tablets, Internet servers (physical side) and processing algorithms (cyber side) conform a CPS. It evolves and improves over time thanks the millions of requests and interactions (10 billion a week according Apple) between the users and intelligent algorithms. Other example of CPS can be found in the energy sector where the electrical network formed by smart meters, transformers, transmission lines, power stations and control centers conform the so called “Smart Grid”.
The same philosophy can be applied at industrial environments where IT technologies are deployed at different levels of complexity. The fast deployment of IoT solutions together with cloud computing solutions connected through Big Data Analytics open the door to the so-called Industrial analytics. Better than providing theoretical explanations, some examples of the CPS applications at manufacturing environment will be more illustrative:
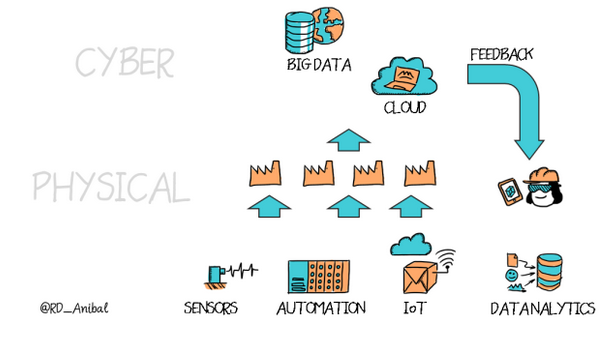
- CPS for OEM manufacturers where the key components (e.g. industrial robots) will be analyzed in real time measuring different internal signals. The advantages will be multiple. The OEM manufacturer will be able to analyze each robot usage and compare it with other robots in the same or different factories. They will be able to improve the next generation of robots or give advice for maintenance and upgrades (both hardware and software).
- CPS for operators: a company providing subcontracted services (e.g. maintenance) will be able to gather information on-field through smart devices to optimize their operations like for example controlling spare parts stock in a centralized way instead of having to maintain multiple local stocks across different sites.
- CPS for factories: gathering on-field information from manufacturing lines (e.g. time cycle) it is possible to build virtual models of the factories and create off-line simulations to aid in decision support (e.g. process optimization) or study the impact of changes in the production lines (e.g. building a new car model in the same line) before deciding new investments.
The combination of physical and virtual solutions open the door to limitless possibilities of factories’ optimization.
- Behind the Curtain: Explainable Artificial Intelligence - 12 July 2024
- Digital Twin: Industry 4.0 in its digitised form - 9 October 2023
- Artificial Intelligence, an intelligence that needs non-artificial data - 16 December 2022