Researchers are increasingly confronted with situations of “digitalise” something that has not been digitalised before, temperatures, pressures, energy consumes,etc. for these cases we look for measure systems or a sensor in a commercial catalogue: a temperature probe, a pressure switch, a clamp ammeter for measuring an electric current, etc.
Sometimes, we find ourselves in the need of measure “something” for which you can´t find commercial sensors. This can be due to they aren´t common measure needs and there isn´t enough market for these type of sensor or directly, doesn´t exist commercial technical solutions available for different reasons. For example, it could be necessary to measure characteristics such as humidity of solid matter currents, or characteristics only measurable in a quality control laboratory in an indirect way and that needs a high experimentation level.
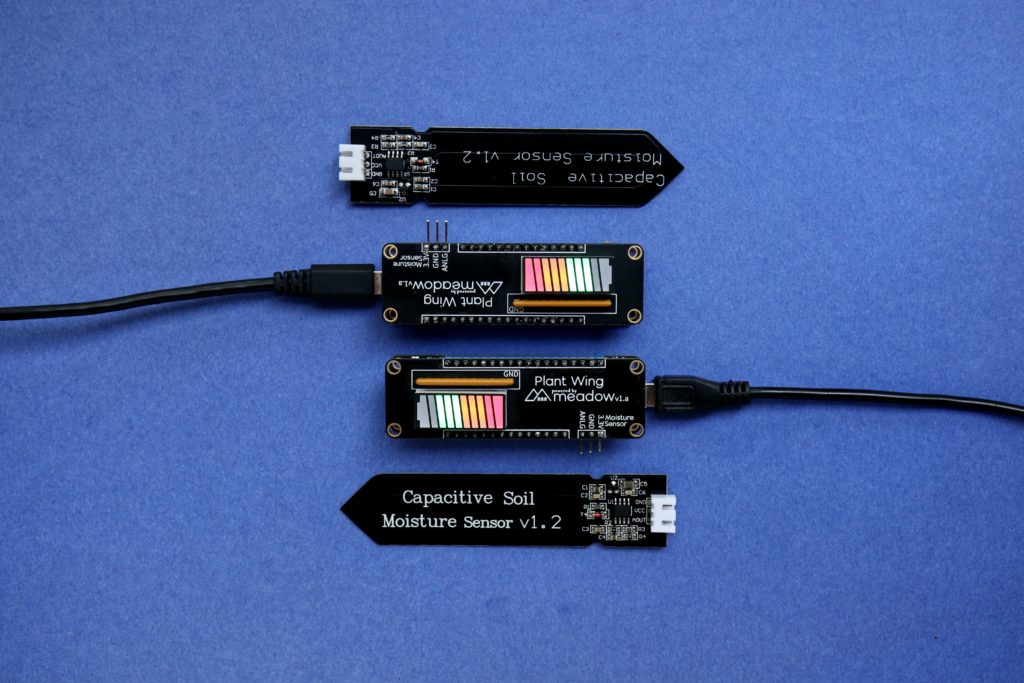
Also, sometimes, characteristics are required to be measured in very harsh environments due to high temperatures, as it can be melting furnace, or environments with lots of dust that saturate any conventional measure system and it may sometimes be necessary to evaluate a characteristic that is not evenly distributed (for example, quantity of fat in a meat piece, presence of impurities). Other factor to take into account is, that not always possible to be installed a sensor without interferences in the manufacturing process of the material that we want to measure, or the only way is taking a sample to realise an analysis out of the line and obtain a value or characteristic time after, but never in real time.
In these situations, it is necessary to resort to custom-made solutions that we call smart sensors or cognitive sensors. Apart from calling them sound exotic or cool, these are solutions that need to use a series of “conventional” sensors together with software or algorithms, for example, artificial intelligence, that process the measurements returned by these commmercial sensors to try to give as accurate an estimate as possible of the quality we want to measure.
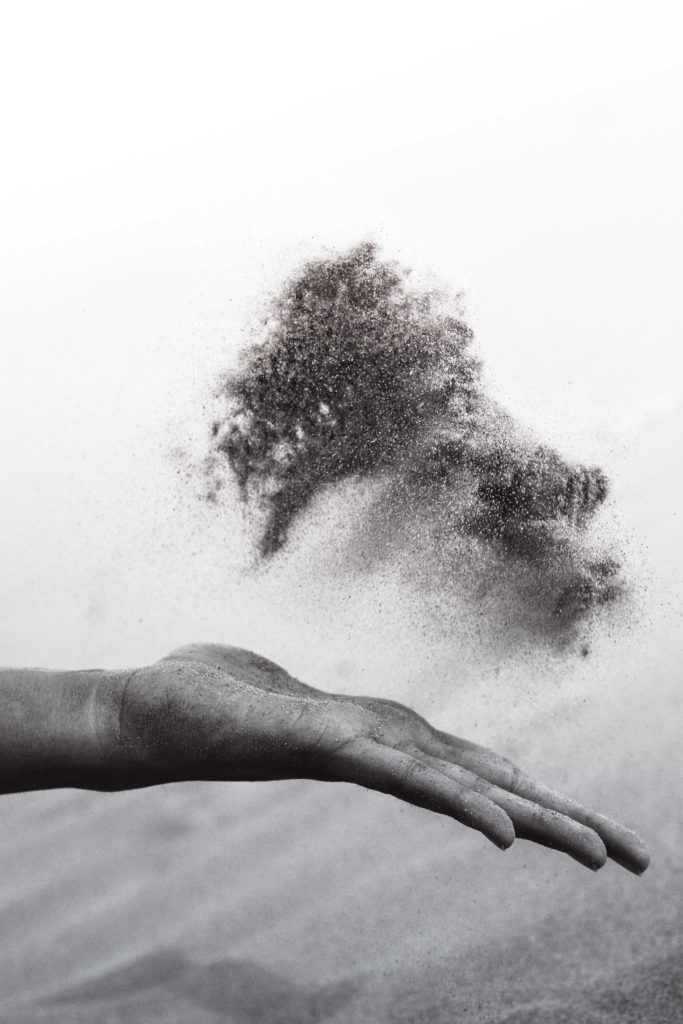
Nowadays we are developing these types of smart sensors for different process industries such as asphalt manufacturing, steel billet and bars or pharmaceutical industry (e.g. pills) in the framework of the European Project CAPRI.
For example, in the manufacture of asphalt, sands of different sizes need to be dried before they are mixed with bitumen. During the continuous drying process of these sands, the finer sand size, called filler, is “released” in the form of dust from larger aggreggates and this dust needs to be industrially vacuumed using what is called a bag filter. Nowadays, the drying and suction of filler is done in a way that ensures that all the filler is extracted. The disadvantage of this process is that it is actually necessary to add additional filler when mixing the dried sands with the bitumen, because the filler improves the cohesion of the mix by filling the gaps between the sand grains. All this drying and complete suction of the filler entails an energy cost that, in order to try to minimise, it would be necessary to have a measure of the filler present in the sand mixture. Today, this measurement is obtained in a punctual way through a granulometric analysis in a laboratory with a sample of the material before drying.
Within CAPRI Project we are working on the complex task of being able to measure the flow of filler sucked in during the drying process. There is no sensor on the market that are guaranteed to measure a large concentration of dust (200,000 mg/m3) in suspension at high temperatures (150-200ºC).
Within the framework of the project, a solution to this problem has been developed, you can consult the laboratory results in the research article recently published in the scientific journal Sensors (“Vibration-Based Smart Sensor for High-Flow Dust Measurement”)
The development of this type of sensors requires various laboratory tests to be carried out under controlled conditions to verify the feasibility of this solution and then, also under laboratory conditions, to carry out calibrated tests to ensure that it is possible to estimate the true flow of filler sucked in during the sand drying process. CAPRI Project has successfully completed the testing of this sensor and others belonging to the manufacture of steel bars and pharmaceutical pills.
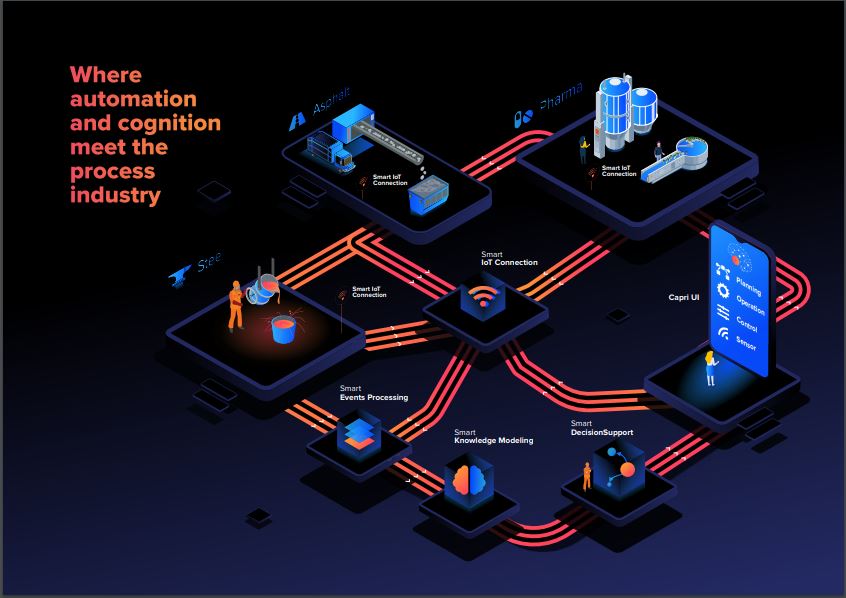
The Project in its commitment to the open science initiative promoted by the European Commission has published in its Zenodo channel, different results of these laboratory tests that allow us to corroborate the preliminary success of these sensors pending their validation and testing in the productive areas of the project partners. In the near future we will be able to share the results of the industrial operation of this and other sensors developed in the project.
Co-author
Cristina Vega Martínez. Industrial Engineer. Coordinator at CAPRI H2020 Project
- Behind the Curtain: Explainable Artificial Intelligence - 12 July 2024
- Digital Twin: Industry 4.0 in its digitised form - 9 October 2023
- Artificial Intelligence, an intelligence that needs non-artificial data - 16 December 2022