
A journey through production
Imagine if every product that reaches your hands could explain its story: where it comes from, what materials it was made with, what processes it went through, how its quality was guaranteed and under what conditions it was transported to its destination.
We live in an era in where information is everything. However, in the industrial world we still let valuable data get lost in siloed systems and time-sensistive decisiones. What if we could make that data visible, useful and connected?
Today, thanks to technologies such as Industry 4.0 and real-time capture systems, production plants generate more information than ever before. But having dat is not enough. The key is structuring, interpreting and connecting it. Turning disparate data into useful knowledge is the first step toward truly intelligent digital labeling.
This is precisely what the European project bi0space is seeking: to develop a digital labeling system for bio-based products that allows each batch to be traced from origin to delivery. This system not only collect technical information ont raw materials, processes and quality controls, but will also include logisitcs data, transportation conditions and environmental KPIs.
Why it is necessary the digital labelling?
In today’s industrial processes, much of the key information about a product’s manufacturing is scattered across different platforms or unstructured. This makes complete traceability of what happens in the plant difficult and, consequently, complicates operational decision-making, continuous improvement, and the justification of sustainability and quality standards. In the context of bio-based production, where materials can vary depending on the supplier, harvest, or process, having control over each stage of the product’s lifecycle becomes especially important. Hence the need to establish a system that allows all this information to be collected and accessed in a unified and accessible manner.
What type of information will be collected?
The digital labeling system being designed at biOSpace includes five essential blocks of information:
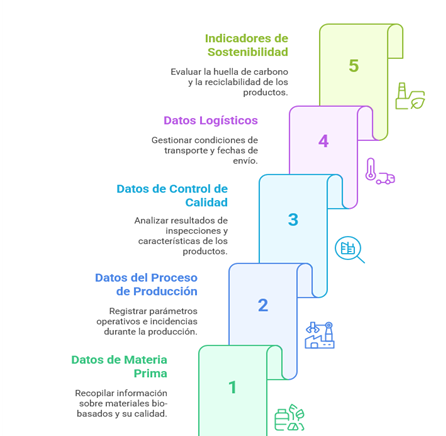
All this data is linked by a unique digital identifier that accompanies the product throughout its entire journey, from entry into the factory to exit. This label is progressively completed, adding information as the product goes through different stages of the process: raw material reception, processing, quality control, packaging, transportation, etc.
This modular identifier structure allows for precise tracing of the product´s journey and condition at each stage, ensuring all relevant information is connected in a clear and structured manner.
What can be reach thanks to the integral traceability?
The value of this information lies not only in its storage, but also in its practical use, tailored to each need. Therefore one of the goals is to enable the system to be accessed from internal dashboards that help plant staff make decisions in real-time, and that at the same time to be integrated into broader digital environments, such as management systems or digital twin platforms.
Furthermore, the same digital label can offer different levels of information depending on the profile of the user consulting it. An operator can view technical data on the process or quality controls, while a sutainability manager can acces environmental KPIs, and an end consumer can view an accesible summary of the product´s origin, characteristics, and traceability.
This detailed traceability will also contribute to what is now becoming known as the digital product passport, a tool that is gaining importance within the framework of European policies toward a more transparent and circular economy.
“What we do with our data today sets the course for what we will do with our products tomorrow”
Although this solution is still in the design phase, it´s based on a simple but important question: what are we doing with all the information already generated in our factories?
In several cases, data exists, but it´s not connected, shared, or simply not used. This project seeks precisely that: to make sense of it, organize it, and make it availabke to those who need it, from the operator who manages a batch to the strategic decision-maker or the persona who, at the end of the chain, consumes the product.
It´s not about incorporating technology as a trend, but rather about using it with criteria. It´s about building tools that allow us to better understand what we produce, how we do it and what impact it has, at a time when traceability, sustainability and transparency are no longer options, but rather conditions for continued progress.