With this post, I would like to try to show a very clear example where, the intelligent use of a suitable artificial vision system can solve a major problem in a production line at a reasonable price.
The body of our vehicle consists of a multitude of metallic pieces, each with its own requirement. The automotive industry manufactures these parts through a laminating sheet forming process called stamping. In this process a metal sheet is placed on a matrix, it is fixed and later, a punch pushes the sheet towards the matrix generating the desired cavity.
Depending on the temperature of the steel blanks two types of stamping are defined: cold stamping and hot stamping. In this case, we will focus on the hot stamping, which is applied mainly in elements of high structural requirement, such as reinforcements, pillars, etc.
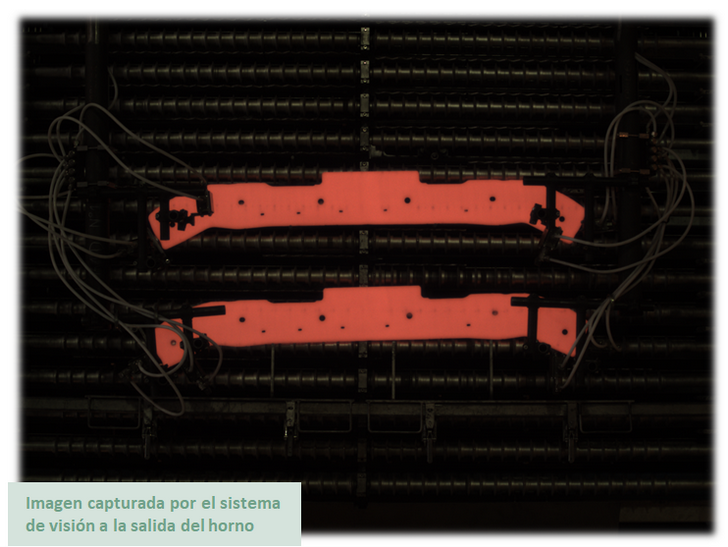
In this process the steel blanks is heated above the austenization temperature, obtaining a high ductility and then proceeding to a rapid cooling to achieve the martensitic hardening of the sheet. The pieces obtained reach high resistance, complex shapes are obtained and the effects of springback are reduced. This allows, among other things, to improve the passive safety of our cars and reduce their weight.
In this manufacturing process, the steel blanks leave the furnace at high speed, at a temperature around 900-950 ºC, they stop abruptly in a fixed position and, later, a robot collects them to introduce them in the press as quickly as possible , In order to avoid its cooling before the press stroke.
The problem arises from the difficulty of ensuring a fixed position with mechanical fasteners. This is due, among other things, to the speed of the line, the great variety of references, the high temperatures of the steel blanks (which cools very quickly at the point where there is a contact) and the internal characteristics of the furnace (which can measure up to 30m).
An incorrect position means that the robot fails to pick up the steel blanks, or worse, to pick it up incorrectly and place it incorrectly in the press, producing a wrong press stroke and stopping the line, together with a deterioration of the tools.
In this case, the artificial vision is presented as the best choice to indicate to the robot if the actual position of the steel blanks is correct. The most important task of the vision system will be to correctly segment the steel blanks into the image in order to accurately determine the position of the steel blanks.
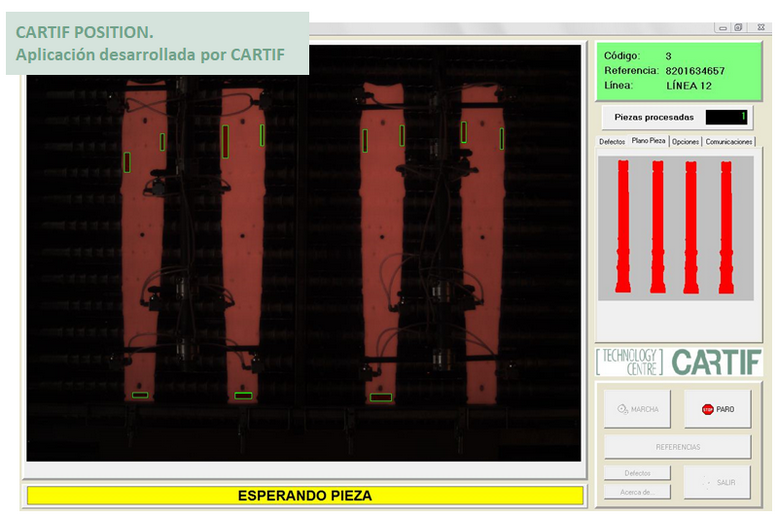
A priori, given the intense infrared radiation emitted by the plates due to their high temperature, it seems that the easiest alternative to achieve this task is to use industrial infrared cameras. This solution presents two problems: the high cost of these equipments and the low resolution of the infrared sensors.
The working area in which the steel blanks are positioned is very wide, due to the size of the parts and because in many cases it is worked in batches, handling up to four units simultaneously. Given the low resolution of these sensors, it is necessary to use several cameras to increase the precision with which the position is defined.
From CARTIF we have been developing more economical solutions, using industrial cameras within the visible electromagnetic spectrum with a greater sensitivity in the infrared range. The resolution of these cameras is much higher than that of the infrared cameras which allows to increase the accuracy of the measurements.
This has allowed companies such as Renault to obtain a robust and configurable system that avoids undesirable stops of the line and extends the useful life of its tools, which leads to a considerable improvement in the production line.
- Terahertz technologies in industry - 31 March 2023
- Robust solutions with simple ideas - 26 August 2022
- Hardware and software ‘easy-to-use’ - 9 March 2018