Machine vision is one of the enablers of Industry 4.0 with increased integration in production lines, especially in the quality control of products and processes. In recent years, a real revolution is taking place in this field with the integration of Artificial Intelligence in image processing, with a potential yet to be discovered. Despite the limitations of Artificial Intelligence in terms of reliability, results are being obtained in industry that were previously unthinkable using traditional machine vision.
The purpose of this post is not to talk about the possibilities of Artificial Intelligence, as there are many blogs that deal with this task, the purpose is to highlight the potential of traditional machine vision when you have experience and develop good ideas.
Machine vision is not just a set of algorithms that are applied directly to images obtained by high-performance cameras. When we develop a machine vision system, we do so to detect a variety of defects or product characteristics. Our task is to select the most appropriate technology and generate the optimal conditions in the scene in order to extract the required information from the physical world from the captured images. There are many variables to consider in this task: the characteristics of the lighting used in the scene; the relative position between the acquisition equipment, the lighting system and the object to be analysed; the characteristics of the inspection area; the configuration and sensitivity of the acquisition systems, etc.
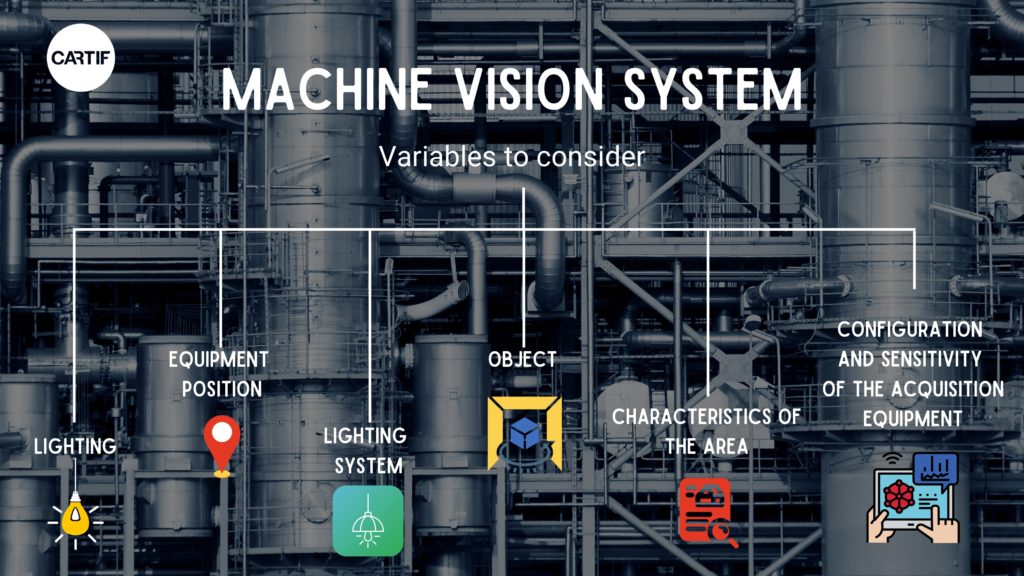
This knowledge can only be acquired from experience and we can highlight that CARTIF has been providing this type of solutions to the industry for more than 25 years.
As a representative anecdote of the importance of experience, I would like to highlight a case that was given to us in an automative components factory.
The company had installed a high-performance commercial vision system whose objective was to identify various parts based on colour. After several failures, we were asked to help configure the equipment, but instead of acting on these devices, we worked on changing the lighting conditions of the scene and simply turned the spotlights around and placed panels to obtain diffuse lighting instead of direct lighting. This solved the problem and the vision reached the level of reliability required by the client.
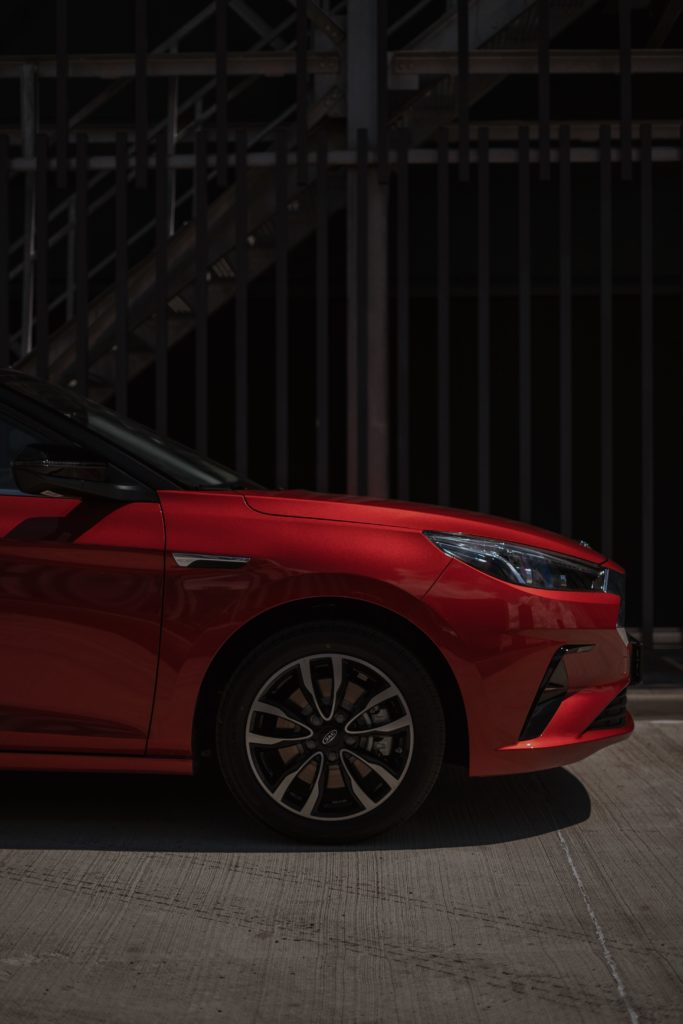
In this post, I would like to highlight an important case of success in the automative industry that has had a relevant impact on its production process, this is the SIVAM5 vision system developed by CARTIF and integrated in cold drawing lines of laminated sheet metal.
As we all know, the surface quality of the vehicle´s exterior is key for users, which is why companies in the automotive sector have to make a significant effort to detect and correct the presence of defects in the bodywork of their vehicles. Most of these defects occur at the stamping stage, but considering the inconsistency of the colour of the sheet metal and the generation of diffuse reflections, in some cases these defects go unnoticed to the body assembly stage and then to the painting stage, after which they become noticeable. This means that a small defect not detected in time translates into a large cost for the production of the vehicle.
To detect these defects at an early stage, we have developed an innovative machine vision system to detect the micro-cracks and pores that are generated in the cold stamping process of rolled sheet metal. This is a clear example of a robust solution based on a simple idea, “the passage of light through the pores of the sheet metal”, but where a great technological effort has been made to implement the idea in the production line. To this end, various optical technologies have been combined with the development of complex mechanical systems, resulting in a high -performance technological solution, capable of carrying out an exhaustive inspection of the critical points of the sheets in 100% of the production and without penalising the short cadence times that characterise press lines.
Thanks to its excellent resistance to vibrations and impacts, its great adptability for the integration of new references and its reliability in the detection of defects, a robust, flexible and reliable solution has been obtained. Based on a simple idea, a robust solution has been implemented in the production process of large companies in the automotive sector, such as Renault and Gestamp, where it has been operating without updates for more than 20 years, working day and night.
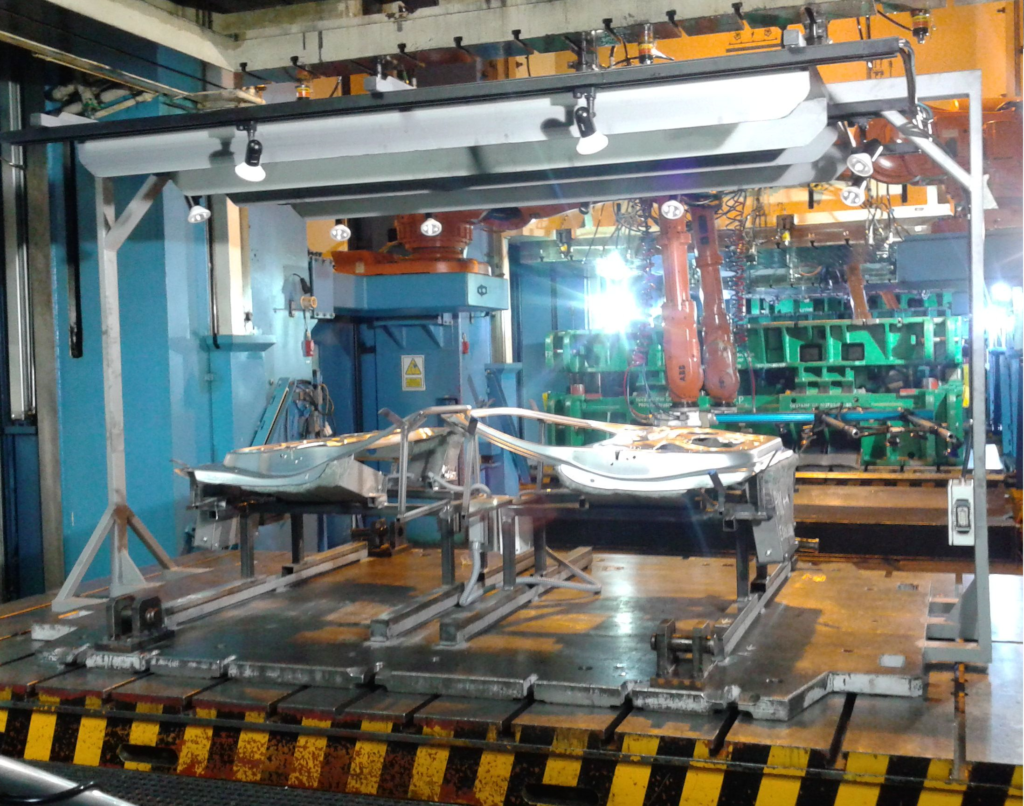
- Terahertz technologies in industry - 31 March 2023
- Robust solutions with simple ideas - 26 August 2022
- Hardware and software ‘easy-to-use’ - 9 March 2018