Low cost alternative innovations. The barometer and how to think outside the box
I finished my previous post commenting how an ILM approach –to disaggregate energy consumption in a factory- can be an unbeatable challenge, financially, for those factories with highly distributed energy consumption.
The commercial market offers several alternatives for industrial measurement systems, designed by the main equipment manufacturers such as SIEMENS, ABB, SCHNEIDER, … capable of providing a hyper-exhaustive follow-up (several measures per second) of the energy consumptions of the different elements in a production chain. However, the cost of the necessary hardware, -the required computer and communications installation-, or the cost of the software licenses make such systems quite expensive. The consequence is that nowadays, they keep being a luxury only available to the large multinationals that also have several similar factories in different locations and, therefore a better purchase negotiation capacity and an easy and high internal replicability. In addition, its production processes are highly automated and computerized through the latest generation MES (Manufacturing Execution System) systems. They already have the necessary IT and communications infrastructure. They just lack the investment in hardware and the “upgrade” of their software licenses.
For other small and medium-sized factories, these solutions can mean “using a sledgehammer to crack a nut”, so that the investment in monitoring will never be profitable (in terms of produced savings). However, these types of factories are increasing their interest in optimizing their energy costs, but employing a reasonable economic investment more appropriate to their billing volumes.
Every science student will have heard the supposed anecdote of Niels Bohr and the barometer in one of its many versions. Although the anecdote of Bohr and the barometer is not real but invented, the moral of trying to think differently when solving a possible problem is more relevant than ever. The difference is that we now call it “thinking outside the box“. The question now is not how to measure the height of a building with the help of a barometer, but, how the measurement and monitoring of energy consumption of a factory could be developed without spending the whole sum of the factory one-year investment budget ?
The answer, as in the problem of the barometer, is not unique, as it will depend on each particular factory. Fortunately, the IOT revolution is producing economies of scale in some of the necessary components. Continuing with the ‘Star Wars’ tribute, the low cost monitoring energy consumption systems can be compared to an X-wing starfighter formed by the following four wings:
- The lower cost of electronics, which is allowing the development of new low-cost non-invasive sensors such as Hall effect-based electric current sensors, ultrasonic flow sensors, or infrared temperature sensors.
- The open source hardware-software platforms for signals capturing and processing through low cost devices like Arduino, Raspberry Pi and others.
- The emergence of new wireless communication protocols oriented to the M2M (Machine To Machine) communication with characteristics of low bandwidth and energy consumption and high resistance to the interferences, like Zigbee, BT LE or Wi-Fi HaLow.
- Software systems for storage and processing all the recorded data, for example the database systems, the multiple indicator reports automatic calculation tools and the use of displays showing the current values of the most important parameters. Both, residents on physical servers located on the factory intranet, or virtual cloud rented servers.
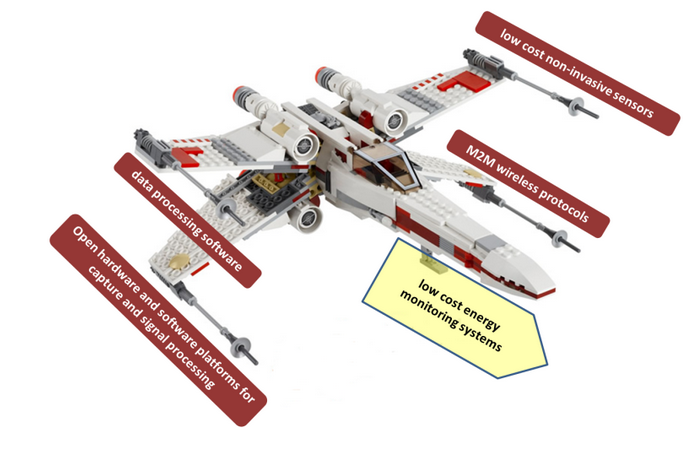
These new technologies are not yet mature and obviously the industry can be very reluctant to use them. If there is something that scares a production or maintenance manager those are the experimental systems that have not been tested previously for years. However, it is necessary to remember that we are not talking about modifying the control systems of processes and machines, but about deploying a parallel system throughout the factory that allows the monitoring and records the energy consumption of the main elements and production systems. We are talking about the detection of possible energy inefficiencies. We are talking about its correction and the corresponding economic savings. And we are talking about doing so with a reasonable investment cost, that is, that an SME can afford it.
- Efficiency Wars (Episode VI) – The Return of Bohr - 25 July 2017
- Efficiency Wars (Episode V) – The ROI strikes back - 20 June 2017
- Efficiency Wars (Episode IV) – A new (efficiency) hope - 25 May 2017