En anteriores posts, el mantenimiento predictivo fue mencionado como uno de los principales habilitadores digitales de la Industria 4.0. El mantenimiento, ligado a la revolución industrial, sin embargo, nos ha acompañado en nuestra evolución como seres humanos.
Desde la prehistoria, nuestros antepasados han construido herramientas que sufrían desgaste y que, a veces, se rompían sin previo aviso. La solución era simple: tallar una nueva herramienta. Al crear mecanismos más elaborados (e.g. rueda de madera), la alternativa natural al desecho se convirtió en la reparación a cargo del artesano. Los telares mecánicos de la Primera Revolución Industrial eran aún más complicados de reparar por lo que surgieron oficios específicos que evolucionaron hacia los operarios de mantenimiento actuales. Durante esta evolución, el desgaste y las roturas de piezas sin previo aviso continuaba siendo parte del día a día de las fábricas.
¿Por qué se ha roto de repente este engranaje que ayer funcionaba perfectamente? El cerebro humano puede asimilar conceptos como la linealidad de acontecimientos (estaciones, noche y día, …) o incluso eventos que suceden a intervalos más o menos regulares. Sin embargo, estos imprevistos desquiciaban a los operarios. ¿Cómo podemos asegurarnos de que ese engranaje no vuelva a romperse? La respuesta era biológicamente predecible: “… pararemos la máquina cada 2 días (por ejemplo) y revisaremos el desgaste del engranaje…”
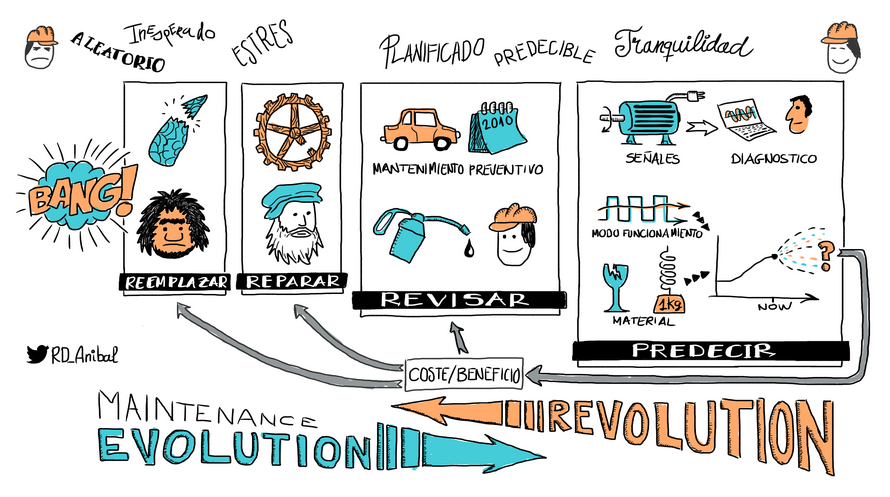
Esta tradición ha derivado en la práctica habitual del mantenimiento que se aplica en la industria y en productos de consumo como, por ejemplo, nuestros automóviles. Nuestro concesionario nos obliga a realizar revisiones periódicas (e.g. cada 10.000 km) para comprobar elementos críticos (frenos, correa de distribución, …) y cambiar piezas con un mayor desgaste (ruedas, filtros …). Esto se denomina mantenimiento preventivo, y se aplica en fábricas u otro tipo de instalaciones (e.g. aerogeneradores) para evitar averías imprevistas. Sin embargo, estas averías no se pueden eliminar (son eso, imprevistas) y es necesaria su reparación. Hablamos de mantenimiento correctivo. El que nadie quiere hacer.
¿Cómo ponerle freno a toda esta catarata de averías inesperadas, gastos de reparación y revisiones innecesarias? Una de las disciplinas en las que más ha trabajado CARTIF desde sus inicios es el mantenimiento predictivo que persigue mitigar (no sería realista asumir que vamos a eliminar lo imprevisto) las averías inesperadas y reducir las revisiones periódicas de las máquinas. De nuevo el mantenimiento predictivo puede explicarse como una respuesta biológica previsible al problema de averías inesperadas. Se basa en la revisión periódica usando señales características del entorno o de la propia máquina que nos puedan indicar de forma anticipada un funcionamiento anómalo. La ventaja de este mantenimiento es que no requiere parar la máquina como en el preventivo. Por ejemplo, un motor eléctrico puede tener un consumo normal cuando funciona correctamente, pero este consumo aumentará si algún elemento del motor sufre algún desgaste excesivo. Vigilando el consumo de forma adecuada podemos entonces detectar averías incipientes.
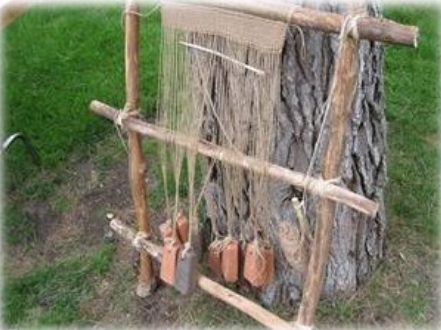
Siguiendo con el ejemplo del motor eléctrico, ¿cuál debe ser la variación mínima de consumo a tener en cuenta para decidir que debemos parar el motor eléctrico y efectuar una reparación? Como en muchas decisiones de la vida, es necesario aplicar un criterio de coste/beneficio, valorando cuánto podemos perder si no reparamos dicho motor frente a cuánto va a costar la reparación. ¿Cómo reducir la incertidumbre en esta decisión? La respuesta es una predicción fiable de la evolución de la avería. Esta predicción estará influenciada por muchísimos factores, algunos de ellos desconocidos (es algo aleatorio como hemos dicho). Sin embargo, los dos principales a tener en cuenta en la predicción son el tipo de evolución de la avería (e.g. la evolución de la avería en una pieza frágil será muy diferente a una pieza más o menos elástica) y el régimen de trabajo al que se verá sometida la máquina (un ventilador encendido las 24 horas del día, frente al motor de un ascensor que arranca y para cada vez que alguien pulsa el botón en un piso). Una predicción fiable permitirá al responsable de mantenimiento elegir, junto con la previsión de carga productiva de la instalación, la opción más beneficiosa, que en muchos casos suele ser la planificación de la intervención de mantenimiento sin que afecte a la producción.
Otro efecto beneficioso del mantenimiento predictivo es que un tratamiento adecuado de las señales medidas ofrece indicios de qué elemento está fallando. Esto se denomina el diagnóstico de la avería y contribuye a reducir la incertidumbre en la acción de mantenimiento más adecuada. Un ejemplo es la medición de vibraciones que permiten diferenciar una avería de un motor eléctrico que tiene un exceso de vibración por un cortocircuito incipiente o debido a un rodamiento dañado. Pero eso es materia de otro post.
- Tras el telón: Inteligencia Artificial Explicable - 12 julio 2024
- Gemelo Digital: la Industria 4.0 en su forma digitalizada - 9 octubre 2023
- Inteligencia Artificial, una inteligencia que necesita datos nada artificiales - 16 diciembre 2022