With the advent of the Industrial Revolution Fourth, some predict a dark future for the worker in a factory where robots and smart manufacturing machines will replace a man who will be limited to just supervise the operation of the factory of the future.
At present the small scale transformations or trends that will define this Factory of the future are already happening. These technological developments and market trends will define its appearance and operation.
The following table lists some of these trends and the expected positive or negative impact for the role (or lack of it) of the worker of the future.
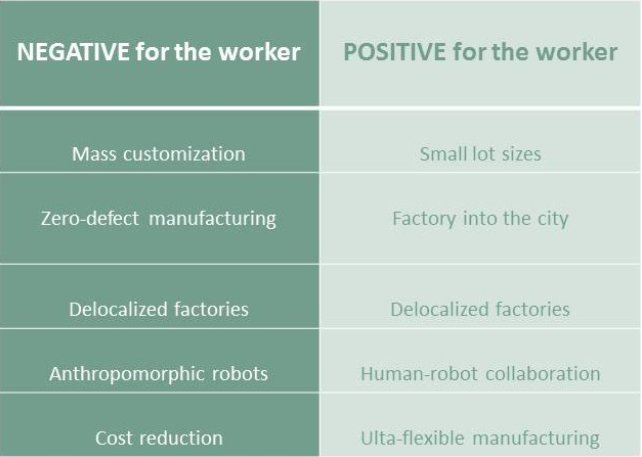
The negative impact of some of these trends is mainly due to the high levels of automation that are needed to achieve the objectives.
What can we do to adapt to these changes and prevent this revolution run over us? The natural response is to worry and choose conservative strategies to stop this revolution at all cost. There has always been a fear of job loss of with any technological breakthrough. For example, with the invention of the printing the scribes nearly disappeared and the invention of the personal computer put in the hands of anyone the desktop publishing. In other cases, with technological breakthroughs new jobs appeared such as those associated with commercial aviation.
During the different industrial revolutions, the role of the worker has been rather passive in terms of how he assimilated and influenced the transformation of their work. With the First Industrial Revolution, artisan work (manual and customized) became a work driven by coal-based energy and steam. With the Second revolution, the work was divided into simple and repetitive operations that allowed the mass production of identical products. With the Third and subsequent digitization of manufacturing (computers, PLC, CAD / CAM …), the obsession with quality and the elimination or reduction of defects introduced new organizational concepts such as lean manufacturing or TPM that tried to reinforce the active role of the worker as responsible for the product and not just a gear in a complicated clockwork. However, at present, with the Fourth Industrial Revolution, the progresses in information technologies and the globalization allow us to attend these changes in a more reactive way.
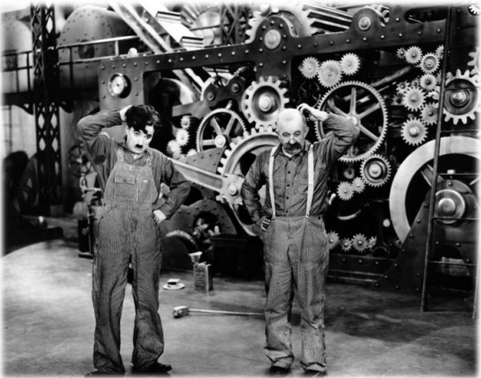
Then, what will be the evolution of the work in the factory of the future? In many aspects, the worker’s role has not changed much since Adam Smith proposed that, as long as the work is divided into operations and paid properly, the matter is settled. However, statistics do not confirm Smith’s premise.
The job satisfaction assessments conducted like the ones done by the US firm Gallup reveal the lowest levels of satisfaction precisely for the US manufacturing jobs (23%) while senior-level positions reach 38%. One might think that the manufacturing salaries in this country are not high enough (if we follow the principles of Smith literally). Well, in the prosperous Germany, the situation is even worse. Only 15% of employees are satisfied with their work.
So, what is the recipe to create more productive and healthy environments? It seems that team managers have a large share of responsibility in this regard: recognize the good job, show that their contributions are valuable, provide adequate tools, listen them and include them in problem-solving. In short: to create a trusty environment for open discussion. Simple, isn’t it?
Not so much, one can not fall in the trap and patronize the worker. There is also needed a personal commitment and a change of attitude. Even in monotonous works are examples of motivated and committed employees. In these cases there is a common denominator: people who are not content just doing the tasks as specified in their job description. Hospital cleaning staff that interact and give support to the relatives of the patient, hairdressers that listen to the client or workers who strive to be more efficient and look for improvements that have the effect of reducing the environmental impact of its activities. Increased autonomy and decision-making capacity result in an increased worker satisfaction. So, how to increase the autonomy in a production line? Precisely technological breaktroughs are the answer to this challenge.
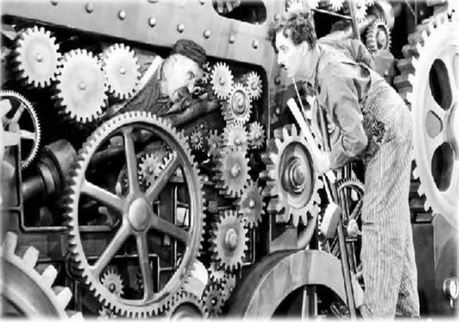
Improvements in automation, adding more robots to perform supporting tasks (internal logistics), collaborative robotics which share space securely with workers and data analytics systems that facilitate more effective decision-making, can be seen as threats to the survival of the role of the worker or as opportunities so this role evolve towards a more active position in the revolution to come.
During a recent meeting I participated, where the vision and priorities of the factory of the future was analyzed, various international experts concluded that the role of workers must evolve from a skills focused in the machinery they use (which will be more and more autonomous and intelligent) to become experts in the manufacturing process in which they are working.
How to protect jobs into the factory of the future? One of the recipes will be to provide the workers tools that result in their increased autonomy and decision making so they can perform their job in a highly flexible environment achieving an adeqaute job satisfaction.
Who knows, maybe in the future, each worker could take to work his own robot as a tool. Thus, the workers with the best “trained” or programmed assistant-robot will the ones with an ensured job.
- Behind the Curtain: Explainable Artificial Intelligence - 12 July 2024
- Digital Twin: Industry 4.0 in its digitised form - 9 October 2023
- Artificial Intelligence, an intelligence that needs non-artificial data - 16 December 2022