Some weeks ago different media reported about the opinion declared by Stephen Hawking, Elon Musk and Bill Gates about the apocalyptic future artificial intelligence might bring us, in which Humanity could be dominated by the machine. Before that terrible day arrives, we can use technology able to resemble human capacities to improve some industrial practices.
One of those technologies allows machines to discover by themselves the different states an industrial process features. Imagine a computer repeatedly fed with values generated by the sensors installed in an industrial process. Non-supervised machine learning techniques make possible the computer finds out the sensor data belong to, let’s say, three classes and moreover it characterises the classes. What the computer could not do is to name the classes, unless a human operator provides it a clue. That is what the operator does when he examines the computer outcome and assigns the names starting, stopping and running, just to follow the example. But in spite of this limitation, the non-supervised machine learning can be successfully used to detect faults or malfunctions that have never been observed in the past. This is what CARTIF did in the hydroelectric sets of a hydroelectric power station.
Hydroelectric sets are at the heart of hydroelectric power stations. Its role is to transform the energy stored in the mass of water retained by a dam into electric power. Each set is monitored and hundreds of variables are registered: electric current and voltage, temperature measured in the mechanical elements, in the refrigeration and water streams used for refrigeration, flows of water and air, etc. In our case, we have the values recorded along two years during which no fault was detected, and so we had not information about the possible faults. The challenge was to design an algorithm able to detect faults.
The solution developed by CARTIF is based on the SOM (Self-Organising Map) neural network, which is capable of non-supervised learning. The network was fed with all the available data and she was able by herself of discovering the possible states the hydroelectric set could present. The network labels the states in an arbitrary way and to give the correct names a human operator has to collaborate. However, this is not required to detect faults. Since the data used for training represent all the possible non-faulty states, any network input that does not fully fit with those states corresponds to a fault.
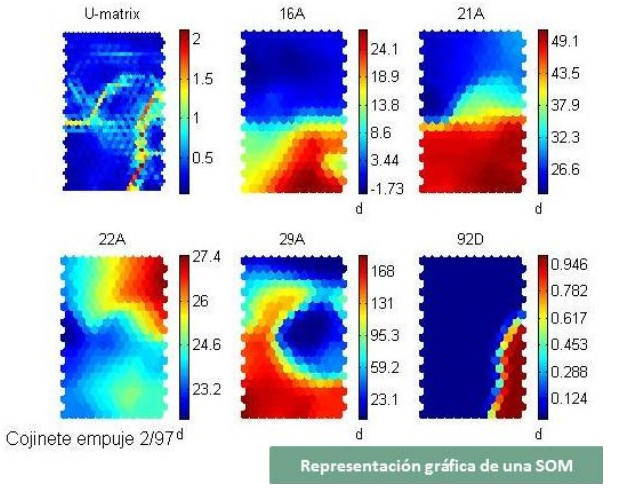
This case can be easily identified by checking the similarity between the sensors signals and the prototypes stored by the neural network. When this similarity is too low, it indicates a fault is occurring.
During testing stage, the algorithm implemented by CARTIF was able to detect an overheating twenty minutes before the plant supervision system raised an alarm. It is important to note that our system used already available sensors and no new ones were required.
So, while we wait for the day machines will rule over us, we may use them to implement intelligent algorithms to improve industrial process supervision with no need for high investments.
- The 28A blackout and the lessons to be learned about the energy transition - 23 May 2025
- We ran out of light - 5 April 2024
- Uncertainties in electricity supply - 15 December 2023