In July 2015 we were surprised by the news that a robot kills factory worker after picking him up and crushing him against a metal plate at Volkswagen plant in Baunatal (Germany). They insisted the death was a result of human error and not any malfunction on the part of the robot. A Volkswagen spokesman stressed that “the robot was not one of the new generation of lightweight collaborative robots that work side-by-side with workers on the production line and forgo safety cages”.
The application of robots in industrial processes is widespread in industry (mainly automotive), where they perform a multitude of tasks, mostly sequential, repetitive and at high speed. Accidents caused by robots are highly unusual. Many robot accidents do not occur under normal operating conditions but, instead during programming, maintenance, repair, testing, setup, or adjustment. During many of these operations the operator, programmer, or corrective maintenance worker may temporarily be within the robot’s working envelope where unintended operations could result in injuries. During normal operation, robots are confined in safety cages precisely to prevent incidents in contact with humans.
Without adequate safety measures traditional industrial robots can cause serious accidents to people by crushing and trapping (occur when a worker’s limb or other body part can be trapped between a robot’s arm and other peripheral equipment, or the worker may be physically driven into and crushed by other peripheral equipment; it can be deadly, as in the case of Baunatal), collision or impact (occur when a robot’s movements become unpredictable and a worker is struck by the robot) or by projection of materials (occur when parts of the robot , tool or product handled, breaks and fly off and hits a worker).
By rules applicable throughout the EU, it has been mandatory to provide a sufficiently large security perimeter to the entire workspace of the industrial robot that prevents access to the robot when in operation. When it will be necessary to enter to this area, the worker must perform some action to stop the robot, facilitating the access. Harmonised standards ISO 10218-1 and ISO 10218-2, “Safety requirements for industrial robots”, contain the minimum requirements for safe operation of these industrial robots.
This “separation” between workers and robots in an industrial environment is weakened through collaborative robots already available on the market (Universal Robots family of robots, ABB’s YuMi, KUKA’s LBR iiwa…) and the new technical specification ISO/TS 15066:2016, “Collaborative Robots”, that specifies the safety requirements for collaborative industrial robot systems and the work environment. The standard describes different concepts of collaboration and requirements needed to achieve them. The ISO standard also points out that the collaborative operation is a developing field and the new technical specification is likely to evolve in future editions.
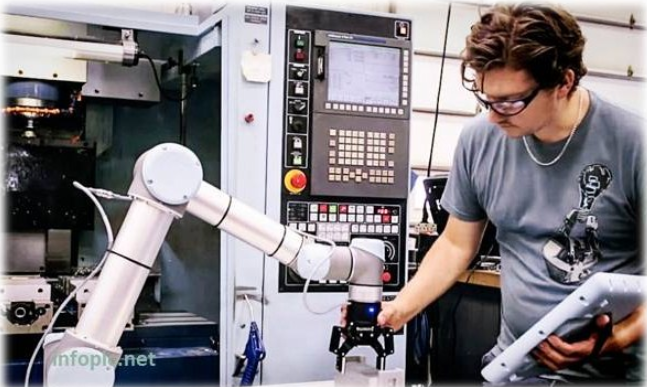
Collaborative robots are designed to operate in a shared workspace with workers without the need for conventional protections, safety cages or safety barriers. The main premise in the design of these robots is the safety of workers (Asimov’s first law of robotics: “a robot will not harm a human being”). These robots are designed to work side by side with workers.
The proximity of workers and robots requires a great safety design based on a combination of mechanical design and control measures, both the manipulator and the workspace. So rather than talking about collaborative robots, in CARTIF we prefer to speak of safe collaboration spaces (collaborative spaces). Besides the robot is safe, so it is the applications and working environments.
To ensure safety can be used different technologies and security measures. Lightweight manipulators without shearing or cutting points, with rounded geometries, smooth surfaces and deformable or elastic components. Speed, acceleration and power can be limited. Current, force, torque sensors can be integrated to detect collisions. Real-time movement of the robot can be adjusted with proximity and tactile sensors. In order to be “aware of the collaborative space” it can be added visual systems based on 2D/3D computer vision technologies.
Usually, collaborative robots are similar to traditional industrial robots but smaller, lighter, less fast and powerful, cheaper and easier to install and configure. These robots do not need to be fast or powerful as they are specially designed to interact with workers. As experts say, in a collaborative space, the worker can bring skills, flexibility and, above all, ability to identify, understand and solve problems, and the robot provides repeatability, accuracy and endurance. Nevertheless, the ISO/TS 15066:2016 standard does not limit the capabilities of the robot in collaborative applications.
- Digitizing the construction to prepare the future - 4 May 2017
- Curie vs Tesla? Autonomous sensors embedded in the pavement - 31 January 2017
- Safety in collaborative robotics - 27 June 2016