In recent years, being the instrumental techniques cheaper and cheaper and the computational algorithms more accesible (even open source) several researchers and consultancy companies are developing new 3D abilities. Laser scanning or photogrammetry techniques are applied to mechanical or structural systems in order to collect some geometric specifications, which may be not available for different reasons.
Although direct engineering process will usually have the technical reports and drawings of the product prior to its building or manufacturing, it is usual that the old factories or buildings are not documented or, if they are, it is quite common that the drawings do not match to project. And even so, the time may have caused differences in the material behavior (chemical attacks, damage, settlements of supports or other common structural pathologies).
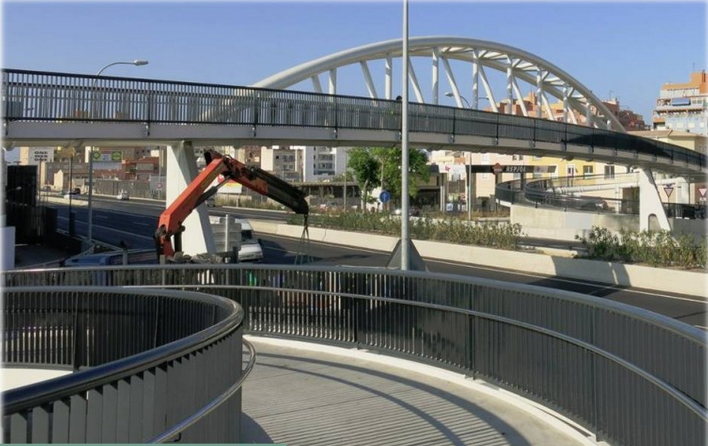
Often the collected data are focused on geometric dimensions and surface characteristics such as roughness and color. One of the most obvious applications is the three-dimensional reconstruction of architectonic buildings, either for rehabilitation or development of augmented drawings (BIM) or for historical or industrial heritage.
Being very useful the geometric data collected, in structural engineering it is necessary to add more information about the characteristics of different building materials, the joints between them and their possible interaction with the supports and the ground.
Fortunately, other enabling technologies to extract some additional information are also becoming more widely available. In this post we will see how using simple acceleration records and identification algorithms together with computational model updating techniques can complete the geometric information so that all technical specifications, necessary to estimate the dynamic behavior of the structure under study, can be obtained. These procedures do not require destructive testing and, even though these tests were viable, they did not provide the required information despite their higher cost.
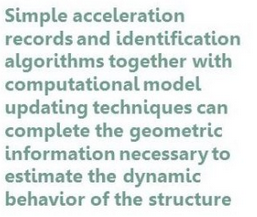
First it should be noted that the geometric data collectedusing 3D techniques, irrespective of dimensional accuracy, refer to a particular state of load on the structure (at least due to the gravitational action) and corresponds to a particular ambient temperature. Both conditions can affect in a significant way when dealing with slender structures such as bridges and pylons. Furthermore these constructs generally experience unavoidable deformations due to environmental actions that can also affect dimensional accuracy of the 3D model.
Second it is interesting to note that in structural engineering and building is usual to use commercial components (proper cross-sections, formworks, pipes, lamps, …) of known discrete dimensions. This enables the possibility of carrying out adaptive scaling for improving the dimensional accuracy or for local refinement. So, it is not necessary comprehensive dimensional records and low cost systems (both instrumental as compact cameras and computer software) can be good enougth.
Considering the above and assuming certain skills for computational modeling, it is posible to create a preliminary model of the structure. On this model, using the finite element method, it is easy to estimate the incremental deformation due to certain loads or thermal actions and through appropriate correlations begin to estimate certain internal parameters (effective density, stiffness, damage, etc.). However, the methodology is especially important when the above information is combined with modal data.
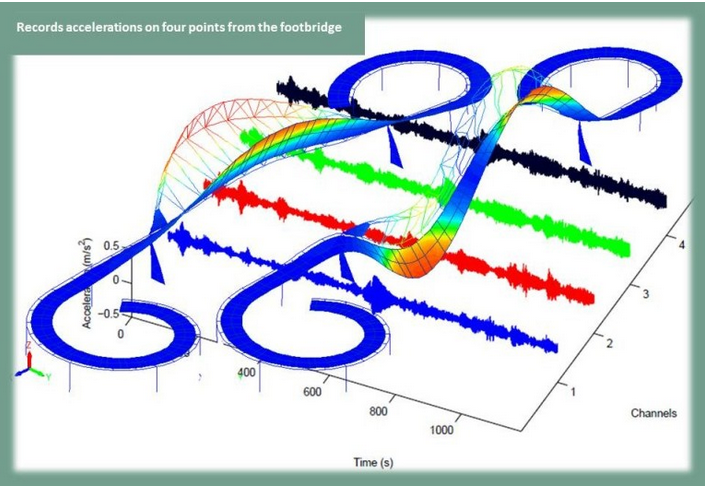
To do this, first thing is to have the experimental eigenmodes (identified through operational modal analysis by post-processing acceleration records under environmental loading) and then select certain parameters of the computational model to be modified. Now it is the turn to adjust the value of these parameters (through optimization routines and depending on the sensitivity of each parameter and its range of reasonable values) to match with the experimental modes to the numerical ones (calculated via FEM). This process should take into account not only the most representative mode shapes but also their modal frequencies and damping.
Once proper values for these parameters are determined, the computer model can be used not only to generate the corresponding technical documentation of the as-built structure but also to estimate their vulnerability to accidental loads, or to evaluate the life-span or to estimate the performance of conservation jobs, among other applications. Those tasks are known as “structural re-engineering”, whose advantages can be matter for other post.
- What could mechanical simulation do for companies? - 26 April 2017
- Product reverse engineering applied to structural dynamics - 4 February 2016