Trying to define the ultimate trend is like trying to choose the perfect camera; once you have purchased the brand new toy, your brother-in-law shows up with the double of megapixels. This time we are talking about Industry 4.0, also known as the fourth industrial revolution. This model seeks the deployment of information technologies within the industry with the main objective of creating a seamless interconnection of manufacturing means facilitating the transition towards a Smart Industry (yes, I know, everything seems to be “smarter” nowadays). Putting the things in context, Industry 1.0 and 2.0 are associated to the first mechanic weaving machine and the first mass-production line (Ford-T), respectively.
Wait a minute, maybe the factory where my brother-in-law works doesn’t have the machines interconnected? The answer to the question is not definitive. In a factory (Industry 3.0) with a reasonable automation level, production means are already interconnected. The current technology solutions in automation establish a predefined hierarchy where the connectivity levels (inside a factory) are already predefined, from the sensor that measures the process state, to the software used at the highest levels of decision-making (e.g. for the business planning or logistics). However, Industry 4.0 vision establishes a hyper-connectivity that goes beyond the factory walls and where production means interact not only with the factory environment itself but along the value chain to which customers, suppliers, logistics etc. belong to.
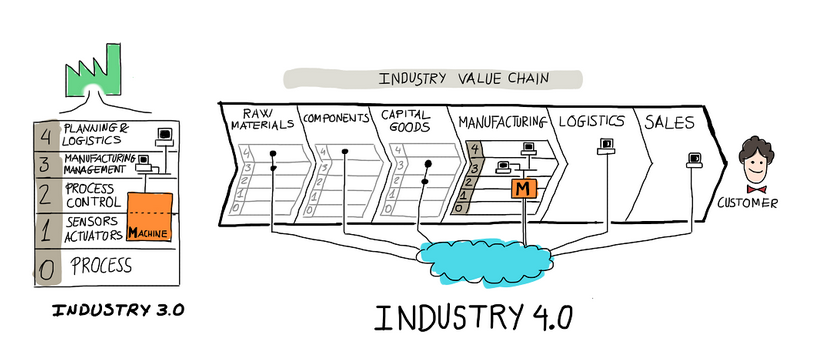
We, as users, are already used to this hyper-connectivity: commercial offers and marketing-in-context messages arrive at our Smartphone every day, personal and professional information is shared (with our implicit permission) through Internet (google your name and tell me the results). So, which are the benefits for a company if they decide to embrace the Industry 4.0 concept? There are many, to mention a few (apart the well-known competitiveness increase):
- A lot of “Likes” (just kidding)
- Continuous and collaborative innovation (along the value chain) at product and process (e.g. my supplier innovates in their machinery and this enhances my manufacturing process).
- Access to new business models (e.g. personalized products)
- A fast reaction and adaptation to changing markets (supply and demand).
The next logical question is if Spanish industry is ready for this 4th revolution. Given the high variety of sectors and companies with different technology maturity levels, the answer is not unique. Something is sure, there are a lot of ready-made technologies: high performance and low cost sensors, embedded systems, data processing and knowledge extraction technologies, encrypting algorithms to name a few. What is missing for Spanish industry then? As with many progresses, these happen faster than we are able to assimilate. We still remember someone close refusing to own a Smartphone. It is the natural man’s resistance (women less) to changes. There is also a training deficit that is already beginning to start mitigating through multidisciplinary programs including robotics, industrial design, programming, etc. However, we cannot wait for these new generations while they get ready (our competitors aren’t waiting). The time is NOW.
The main characters of this revolution are everywhere: big companies as necessities’ generators and main drivers and capital goods manufacturers supplying production machinery for virtually all considered sectors. These capital goods sector have already began a silent “collaborative innovation” process. The lessons learnt from a sector or specific customer, sooner or later, find their way to the next factory. The hyper-connectivity that Industry 4.0 encourages, seeks to accelerate this collaborative innovation process (not only for the capital goods manufacturers). As an example, machinery embedded intelligence will be able to provide real-time status information (useful for the machinery maker and user) to optimize the process (e.g. energy performance, and maintenance) or to inform OEM’s components suppliers (e.g. reliability information). In addition to the information supplying it is expected that smart machines will be able to automatically influence production process to optimize it.
The key concepts for this revolution are varied and with exotic names (the kind my brother-in-law loves): cyber-physical systems, internet of things or big data to name the most well-known. But this is another history.
- Behind the Curtain: Explainable Artificial Intelligence - 12 July 2024
- Digital Twin: Industry 4.0 in its digitised form - 9 October 2023
- Artificial Intelligence, an intelligence that needs non-artificial data - 16 December 2022