Any processing plant – continuous, batch, hybrid – can improve its economic, safety and environmental indicators in two ways: improving its processing equipment or improving the control of those equipments.
The improvement of processing equipment is usually a task that requires large investments, since it almost always involves the acquisition of new processing equipment or in the best case requires expensive remodeling.
On the contrary, these performance indicators can be substantially improved through control, without, in the majority of cases, any investment in new technical means of instrumentation and control. This is because in practically all cases there is a wide margin to improve the performance indicators of a processing plant through its regulation.
The origin of this margin of improvement is multiple. The most common causes are: the control system is not well designed or tuned; due to ignorance or haste, all the benefits of the available control system are not used; the automaton programmer or the process engineer are not control experts; the dynamics of the processes under automatic regulation are not known with the required depth; the design of the plant has not been made under the integrated design approach.
Are also diverse and numerous actions that can be implemented to improve the performance of control loops without any investment and that we will review in next posts, such as: improve the tuning of the regulator, redesign the controller, implement anticipatory compensation of disturbances, enhance the tuning of cascade regulation loops, redesigning or re tuning the level controllers of the buffer tanks if necessary, using a control algorithm advanced available or supportable by the controller instrument, reducing couplings between loops, making a better assembly of the measuring probe, etc.
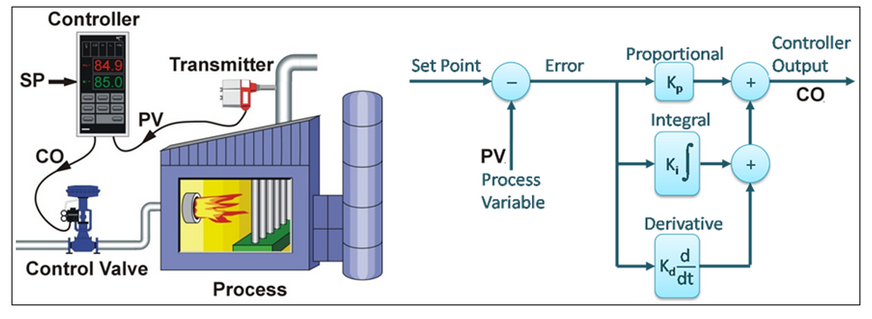
In its vast majority, the processing plants are automated under control structures (basic control, cascade control, split range control, selective control, coupled loops, etc.) based on the universal PID controller, in all its particularizations (P, PI, PD, PID, PI_D, etc.).
Despite its longevity and the development of multiple advanced control techniques, PID control maintains an overwhelming presence in the process industry.
Its extensive use in the industry is such that all the surveys known by the author conclude unanimously, in which more than 95% of the existing control loops are of the PID type. However, also many surveys conclude that a high percentage of the loops with PID control in the world, are operated in manual mode, while another similar percentage operates defectively. For example, as shown in the following figure, in [1] it is reported that only 16% of the PID regulation loops are optimally tuned and their performance is therefore excellent.
There is no doubt that in most cases, the incorrect or poor tuning of the controller can be the cause of the poor performance of the control loop or its irregularities in the operation.
However, it should not be forgotten that automatic regulation systems are holistic systems, and as such they must be analyzed as a whole and not only through the parts that compose them. That is why it is necessary to review the other components of the loop before deciding what action should be exercised on said loop.
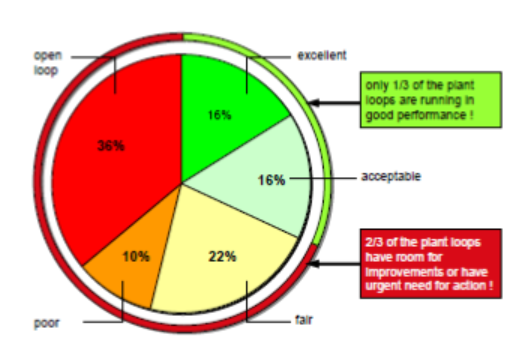
Hence, the procedure of action in all cases, must begin with a field review of all the components of the loop (controller, process, actuator, measurer and communication channels), as well as an analysis of the possibility of coupling with other process loops.
The result of this first phase will determine what concrete action corresponds to perform to solve the poor performance of the automatic regulation loop.
CARTIF offers this service to optimize the performance of the regulation systems of processing plants. The optimization reduces the oscillations and the variability of the production plant, making the regulation system more accurate, faster, more stable and safer, and in this way improving its efficiency, safety, environmental impact and profitability.
In next post, the execution procedure will be described for each of the possible actions, starting with the simplest one, the re-tuning of the controller.
- How to improve your processing plant without large investments? - 27 December 2017
- Fighting with triple A (AAA), the silent enemy - 23 September 2016