The term eco-design is rather known nowadays, but you’ve probably heard little about eco-manufacturing, especially since it’s not a term widely recognized in technical or academic literature. However, it is a concept that has recently started to be used to describe manufacturing practices that centrally incorporate environmental aspects. Well, I’ll go even further, and try to explain what “metal-eco-additive manufacturing” is, a term I just invented to title this.
Forty years ago, Charles Hull’s invention of stereolithography (SLA) gave rise to what we now know as 3D printing – or additive manufacturing. Going one step further, the concept of metal 3D printing emerged after decades of development and experimentation, though its ideation can be attributed to Carl Deckard, a pioneer in Selective Laser Sintering (SLS) about 30 years ago at the University of Texas. Far from its industrial application at the time, its development went hand in hand with advances in new materials and high-power lasers in the 2000s. Although many have heard of processes for metal 3D printing, such as Selective Laser Melting (SLM) or Electron Beam Melting (EBM), it’s worth noting that the technology took 10 more years to reach large-scale industrial production – not just prototypes, as was done during the development phase for sectors like aerospace, automotive, or medical (which had the money for such “toys”).
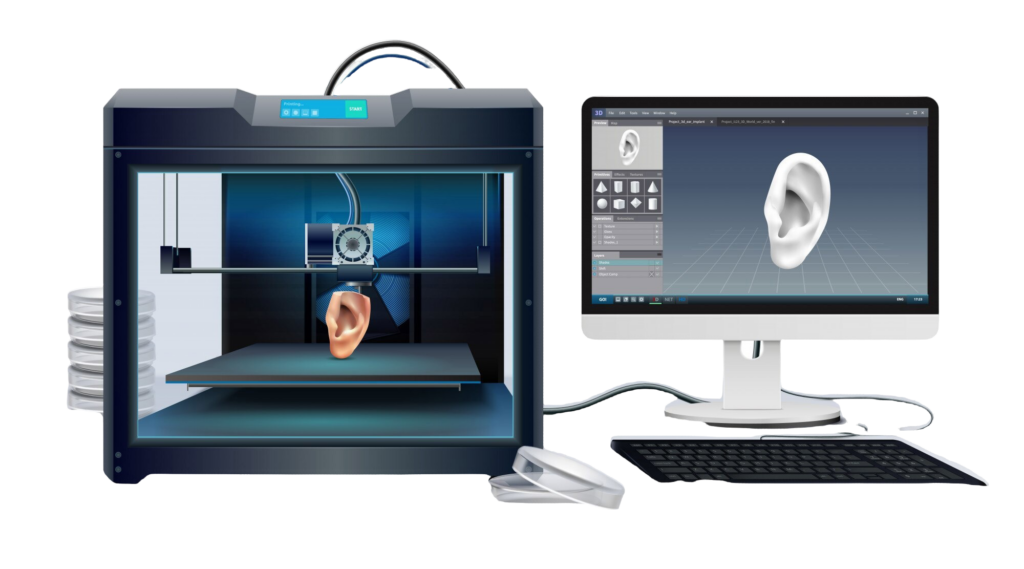
Over the past 15 years, metal 3D printing processes have significantly improved (in precision, resolution, speed, physical properties, quality control, etc.), largely due to the emergence of new materials and their characteristics. On the other hand, methodologies have been created to analyze the efficiency of manufacturing processes themselves, parametric control, automation, and robotics, which directly impact costs, thus enabling the expansion of metal 3D printing applications to other sectors. Currently, these enhanced processes include, for example, Powder Bed Fusion (PBF), Direct Energy Deposition (DED), and metal Binder Jetting.
Well, the thing with additive manufacturing is like any technological process – progress is unstoppable: we don’t make airplanes the same way we did 120 years ago, right? 120 years ago, flying was already a reality (12 seconds and 36.5 meters), but I doubt we would agree to define “flying” the way the Wright brothers did in 1903. Their goal was “simply” to fly and survive. I don’t think they could have imagined that their scientific curiosity would become a key pillar of the global economy, nor did they think about 600-passenger airplanes, certifications governing the industry, or the pervasive existence of spaces for takeoff and landing.
In the same way, Carl Deckard, beyond his scientific interest in mechanical engineering, probably didn’t envision changing the world with his invention. However, just as air transport did, the additive manufacturing of metal parts has had, has, and will continue to have a massive impact globally. We now have new rules of the game and manufacturing possibilities for designs that were impossible until recently (generative designs), as their economic and environmental costs were prohibitive and bordering on madness. For example, if you don’t know how an airplane turbine is made (at least what it’s made from or how long it takes!!), you can’t appreciate the madness I’m referring to… and there are more and more airplanes every day!
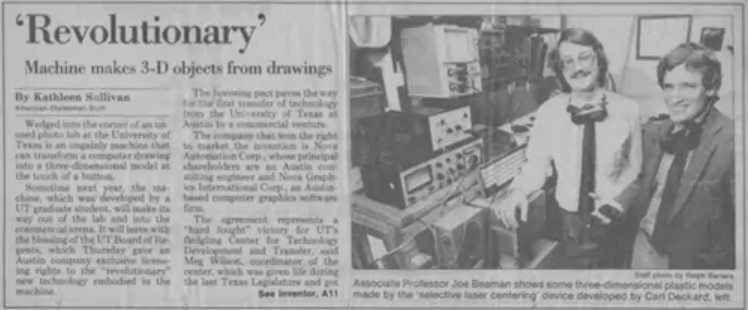
Ecological awareness (so necessary today), the challenge ahead, and the transition to sustainability, will drive the circular economy in the use of metal additive manufacturing (or 3D printing). Or could it be additive manufacturing that will foster environmental sustainability? Or maybe a “virtuous loop” could be created where both fields will feed back into each other, by means of new concepts such as the one that I am coining here as metal-eco-additive manufacturing?
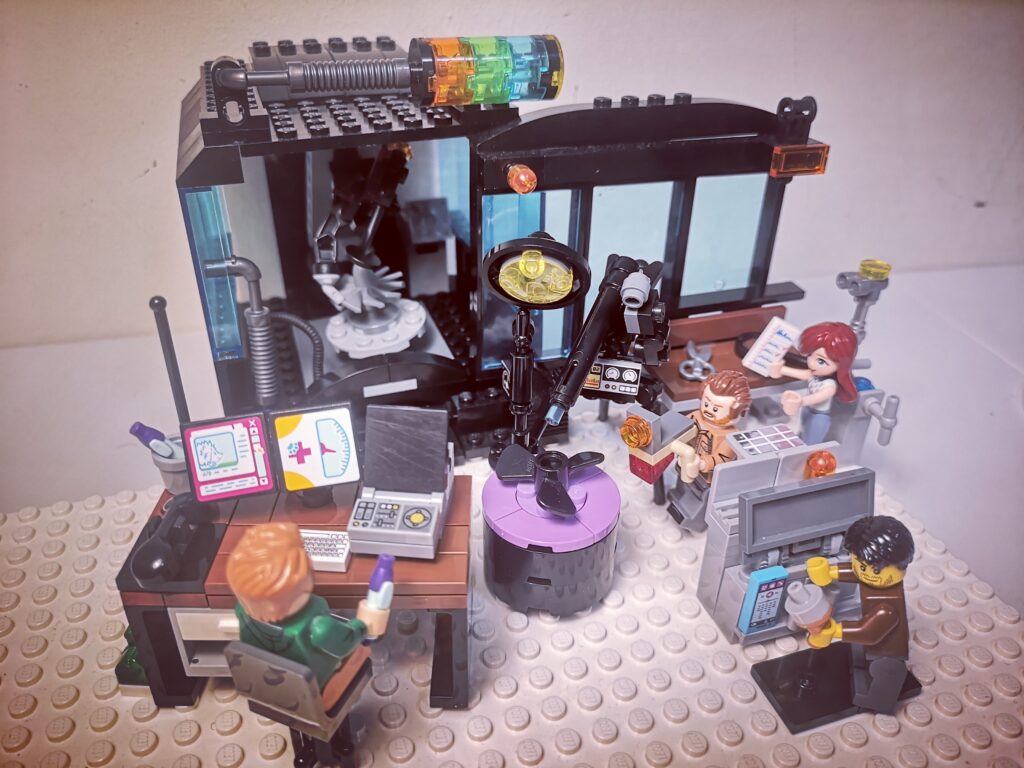
The thing is that everything evolves and new challenges arise; it won’t be enough just to design landing gears that fulfill their mission: apart from ensuring no one dies, they must be competitive. We must (and will be required to) know they were created in the most sustainable way possible and under circularity criteria. How? Well, looking towards the future, let’s imagine that the manufacturing conditions for a structurally responsible part could combine several manufacturing processes, not just one (machining) or the other (additive). Let’s also imagine that we could make parts that, although they could have inadequate finishes due to faster processes, these could be corrected in later treatments with techniques that require less effort. Or even, imagine that, if a part fails, we could refurbish it directly: that is, print what is missing on the same part so that the company using it can repair it in their own facilities. We wouldn’t have to throw away the part! Nor make a new one! We would avoid inventories of parts, storage, or transport of those spare parts, which is highly undesirable…
Well, the combination of additive manufacturing and circularity has a synergy point that will be researched and implemented over the next 4 years through a European project called DIAMETER, which involves more than 20 prestigious entities from 4 different continents. CARTIF is just one of these privileged entities that have already started working to build a bridge between metal additive manufacturing and the circular economy.
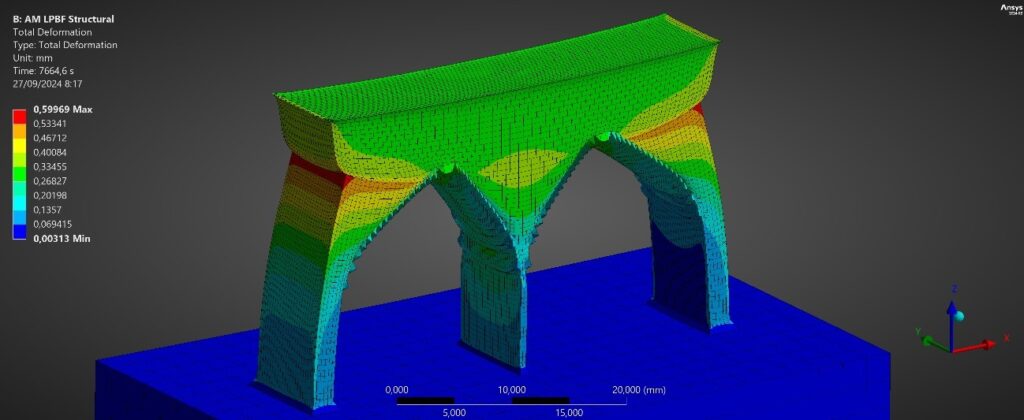
This bridge will be a framework where a series of metal parts used in critical cases across various production sectors will be analyzed, manufactured by different additive manufacturing processes. In DIAMETER, experimental physical results from the manufacturing processes will be compared with computational simulations of the parts in these processes to predict how the parts will respond to different process modifications. These responses (in terms of stress/deformation, among others) will provide mechanical knowledge about the parts and processes in terms of failures, waste, quality, or the need to integrate post-processing (hybrid manufacturing combining additive and subtractive). In short, a combination of possible scenarios and results that must be transformed into quantifiable outcomes under a sustainability approach to feed into an artificial intelligence system that will provide automated, optimal decisions on procedures and configurations in metal additive manufacturing of parts.
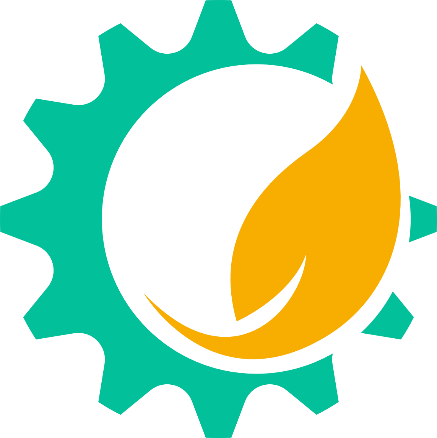
“Feed into an artificial intelligence system that will provide automated, optimal decisions”
“One moment, this is crazy!”
Well, yes, it’s as crazy as machining a 3m³ block of stainless steel on a 6-axis lathe for a week to get an airplane turbine or a hydraulic turbine. Or, seen another way, 500K€ for a week, with the possibility that, if there are errors, the turbine might need to be thrown away and start over from scratch.
But let’s take it step by step. The first thing will be to characterize these manufacturing processes, see how the parts are generated and whether they suffer deviations, inaccuracies, or analyze the quality of the surface itself. For this, artificial vision technology for geometric verification of parts during the manufacturing process will be used, which are technologies in which CARTIF has been working 30 years… and we have much ahead to go in the future!
Co-author
Iñaki Fernández Pérez. PhD in Artificial Intelligence. Researcher at the Health and Wellnes area at CARTIF. He is currently collaborating on several projects that seek to apply cutting-edge technologies (AI, IoT, Edge Computing…).
- How does the term “metal-eco-additive manufacturing” sound? - 27 December 2024
- Beyond strategy. Smart use of engineering expertise. - 23 December 2022
- Infinite progress through finite elements - 30 May 2017