Es de sobra conocido el término ecodiseño, pero seguro que habéis oído hablar poco de ecofabricación, más aún cuando es un término que no está ampliamente reconocido en la literatura técnica ni académica. Sin embargo, es un concepto que se viene utilizando recientemente para describir prácticas de fabricación que incluyen de forma central aspectos medioambientales. Pues voy más allá, a ver cómo os cuento de qué va la fabricación «metalecoaditiva», término que me acabo de inventar para darle título a esto.
Hace 40 años, Charles Hull y su invención de la estereolitografía (SLA) dio paso a lo que ahora conocemos como impresión 3D – o fabricación aditiva. Yendo un paso más allá, aparece después el concepto de impresión 3D de metales, que surge de décadas de desarrollo y experimentación, aunque su ideación se podría atribuir a Carl Deckard, pionero en el Sinterizado Selectivo por Láser (SLS) hace unos 30 años en la Universidad de Texas. Lejos entonces de su aplicación industrial, su desarrollo fue de la mano de más avances en materiales novedosos y láseres de alta potencia en los años 2000. Aunque muchos ya han oído hablar de procesos para impresión 3D de metales, como la Fusión Selectiva por Láser (SLM) o la Fusión por Haz de Electrones (EBM), cabe destacar que la tecnología tardó 10 años más en llegar a producciones industriales a gran escala – y no sólo prototipos, como se venía haciendo en fase de desarrollo para el sector aeronáutico, automotriz o médico (que son los que tenían el dinero para tales «juguetes»).
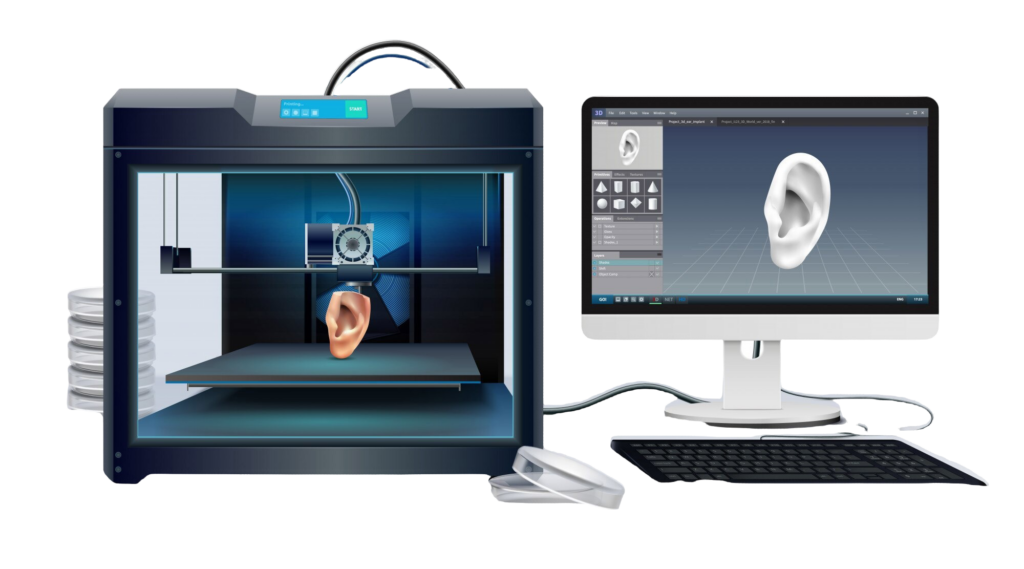
En los últimos 15 años, los procesos de impresión 3D de piezas metálicas han seguido mejorando considerablemente (en precisión, resolución, velocidad, propiedades físicas, control de calidad…), en gran parte por la aparición de nuevos materiales y las características que éstos presentan. Por otro lado, se han creado metodologías para analizar la eficiencia de los propios procesos de fabricación, control paramétrico, automatización y robótica, que repercuten directamente en los costes, y por tanto posibilitan la expansión de la aplicación de impresión 3D de metales a otros sectores. Actualmente, estos procesos mejorados incluyen, por ejemplo, la Fusión por Lecho de Polvo (PBF), la Deposición Directa de Energía (DED) o la fabricación aditiva por Inyección de Metal (Binder Jetting).
Bueno, pues todo esto de la fabricación aditiva es como todo proceso tecnológico – la mejora es imparable: no se hacen aviones ahora como hace 120 años, ¿verdad? Hace 120 años ya se volaba (12 segundos y 36,5 metros), pero no sé si estaríamos de acuerdo en definir volar a lo que hicieron los hermanos Wright en 1903. Su objetivo era «simplemente» volar y salir vivos. No creo que pudiesen imaginar que su curiosidad científica se convertiría en un pilar clave de la economía global, ni que pensasen en aviones de 600 pasajeros, en certificaciones que rigen el sector o la existencia ubicua de espacios para despegar y aterrizar.
De la misma manera, seguramente Carl Deckard, más allá de su interés científico en ingeniería mecánica, no se planteaba cambiar el mundo con su invención. Sin embargo, igual que lo hizo el transporte aéreo, la fabricación de piezas metálicas de forma aditiva ha tenido, tiene y seguirá teniendo un impacto enorme a nivel global. Tenemos ahora nuevas reglas de juego y posibilidades de fabricación de diseños, imposibles hasta hace bien poco (diseños generativos), ya que sus costes económicos y medioambientales eran prohibitivos y rozaban la locura. Por ejemplo, quien no sepa cómo se fabrica una turbina de un avión (¡¡al menos de qué se parte o cuánto se tarda!!), no puede valorar la locura a la que me refiero… ¡y cada vez hay más aviones!
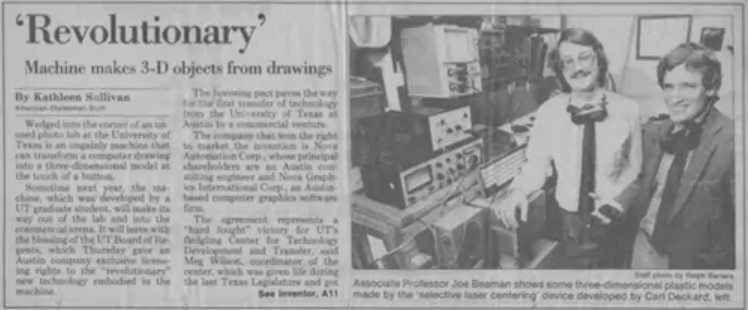
La conciencia ecológica (tan necesaria actualmente), el desafío que tenemos por delante y la transición hacia la sostenibilidad van a impulsar la economía circular en el uso de la fabricación aditiva ( o impresión 3D) metálica. ¿O podría ser la fabricación aditiva quien potencie la sostenibilidad medioambiental? ¿O tal vez se pueda crear un «bucle virtuoso» en las que los dos ámbitos se retroalimenten, por medio de nuevos conceptos como el que yo acuño aquí como fabricación metalecoaditiva?
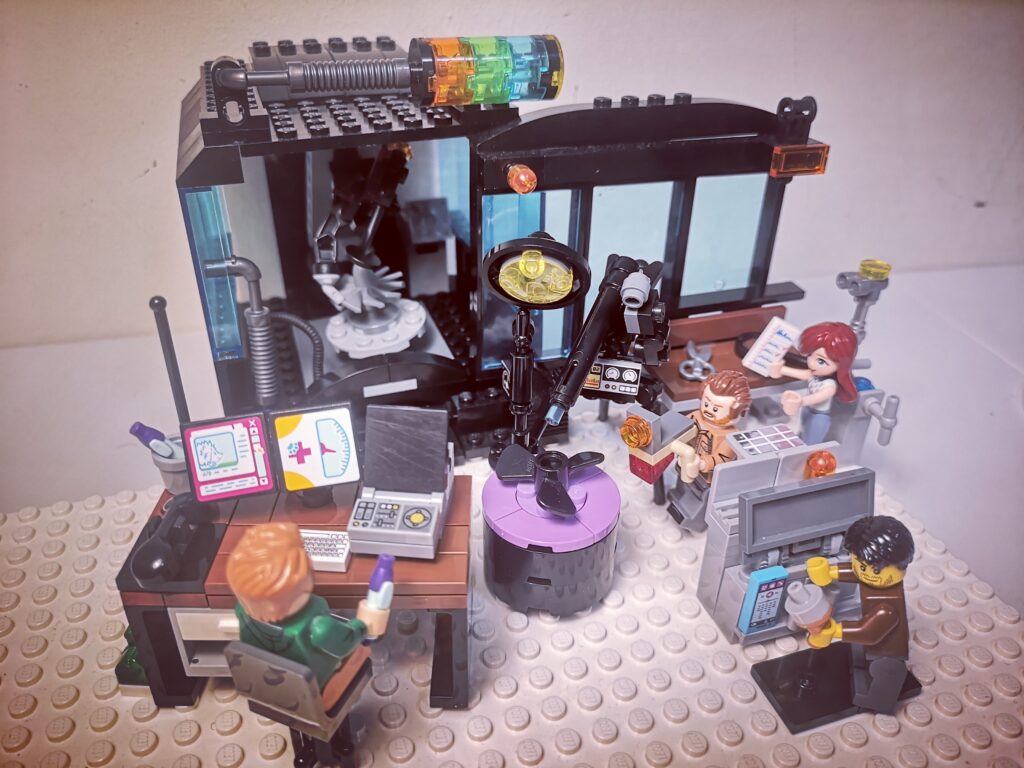
La cosa es que todo evoluciona y nuevos retos entran en contienda; ya no va a valer sólo con diseñar trenes de aterrizaje que cumplan su misión: aparte de que no muera nadie, deben ser competitivos. Debemos ( y se nos va a exigir) saber que han sido creados de la forma más sostenible posible y bajo criterios de circularidad. ¿Cómo? Bueno, mirando al futuro, imaginemos que las condiciones de fabricación de una pieza de responsabilidad estructural pudieran combinar varios procesos de fabricación, y no sólo uno (maquinado) u otro (aditivado). Imaginemos también que fuéramos capaces de hacer piezas que, aunque por las condiciones del proceso (más veloces) tuvieran acabados inadecuados, éstos se pudieran corregir en tratamientos posteriores con técnicas que impliquen un menor esfuerzo. O incluso, que, ante una falla de pieza, pudiésemos reacondicionarla directamente: es decir, sobre la misma pieza imprimir lo que le falta, y que así la misma empresa usuario de la pieza pueda repararla en sus propias instalaciones. ¡No tendríamos una pieza que desechar! Ojo, ¡ni la necesidad de hacer una pieza nueva! No incurriríamos en inventarios de piezas, almacenamiento o transporte de esos repuestos, tan indeseable…
Pues bien, la combinación de la fabricación aditiva y la circularidad tiene un punto de sinergia que va a ser investigado e implementado durante los próximos 4 años a través de un proyecto europeo llamado DIAMETER, en el que participan más de 20 entidades de alto prestigio, de 4 continentes distintos. CARTIF es sólo una de estas entidades privilegiadas que ya han empezado a trabajar en construir un puente entre la fabricación aditiva de piezas metálicas y la economía circular.
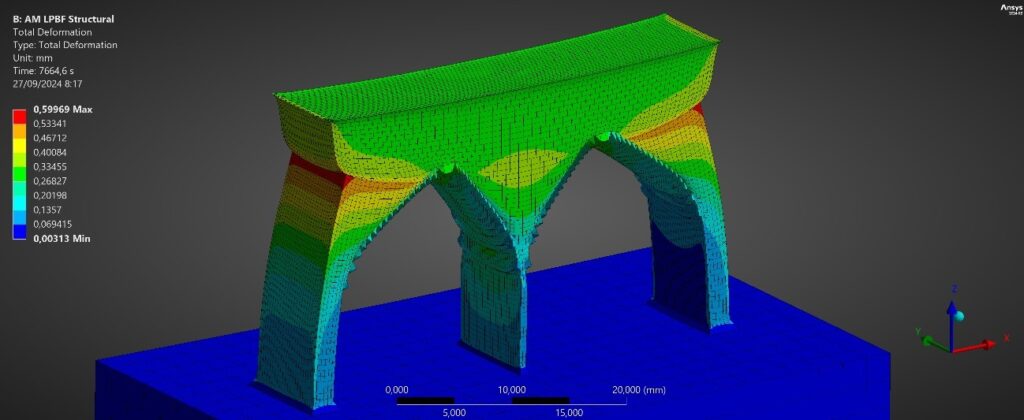
Este puente será un marco donde analizar una serie de piezas metálicas usadas en casos críticos de varios sectores productivos, y fabricadas por diferentes procesos de fabricación aditiva. En DIAMETER, se contrastarán resultados físico-experimentales de los procesos de fabricación frente a simulaciones computacionales de las piezas en esos procesos para, con ello, prever las respuestas de las piezas frente a diferentes modificaciones del proceso. Estas respuestas (de tensiones/deformaciones, entre otros) aportarán un conocimiento mecánico de la pieza y del proceso en cuanto a fallos, desperdicios, calidad, o necesidad de integrar posprocesado (fabricación híbrida combinando aditiva y sustractiva). En definitiva, una combinatoria de posibles escenarios y resultados que deben ser transformados en resultados cuantificables bajo un enfoque de sostenibilidad para alimentar un sistema basado en inteligencia artificial que proporcione decisiones automatizadas y óptimas sobre procedimientos y configuraciones en la fabricación aditiva de las piezas metálicas.
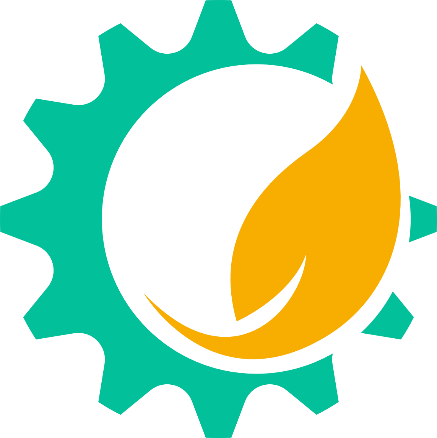
«Alimentar un sistema basado en inteligencia artificial que proporcione decisiones automatizadas y óptimas»
«Un momento, ¡esto es una locura!»
A ver, sí, una locura casi tan grande como tallar (maquinar) un bloque de 3m3 de acero inoxidable en un torno de 6 ejes durante una semana para obtener una turbina de avión o una turbina hidráulica. O, dicho de otra manera, 500k€ durante una semana, con la posibilidad de que, si hay errores, haya que tirar la turbina y volver a empezar de cero.
Pero vamos a ir paso a paso. Lo primero va a ser caracterizar esos procesos de fabricación, ver cómo las piezas a fabricar se van generando y si estas sufren desvíos, imprecisiones, o analizar la propia calidad de la superficie. Para ello se va a emplear tecnología de visión artificial de verificación geométrica de piezas durante el proceso de fabricación, que son temáticas en las que CARTIF lleva trabajando 30 años…¡y lo que nos queda!
Co-autor
Iñaki Fernández Pérez. Doctor en Inteligencia Artificial. Investigador en el área de Salud y Bienestar de CARTIF. Actualmente colabora en varios proyectos que buscan aplicar tecnologías punteras (IA, IoT, Edge Computing..)
- ¿Cómo suena eso de fabricación «metalecoaditiva»? - 27 diciembre 2024
- Más allá de la estrategia. Utilización inteligente de la experiencia en ingeniería - 23 diciembre 2022
- Avances infinitos mediante elementos finitos - 30 mayo 2017