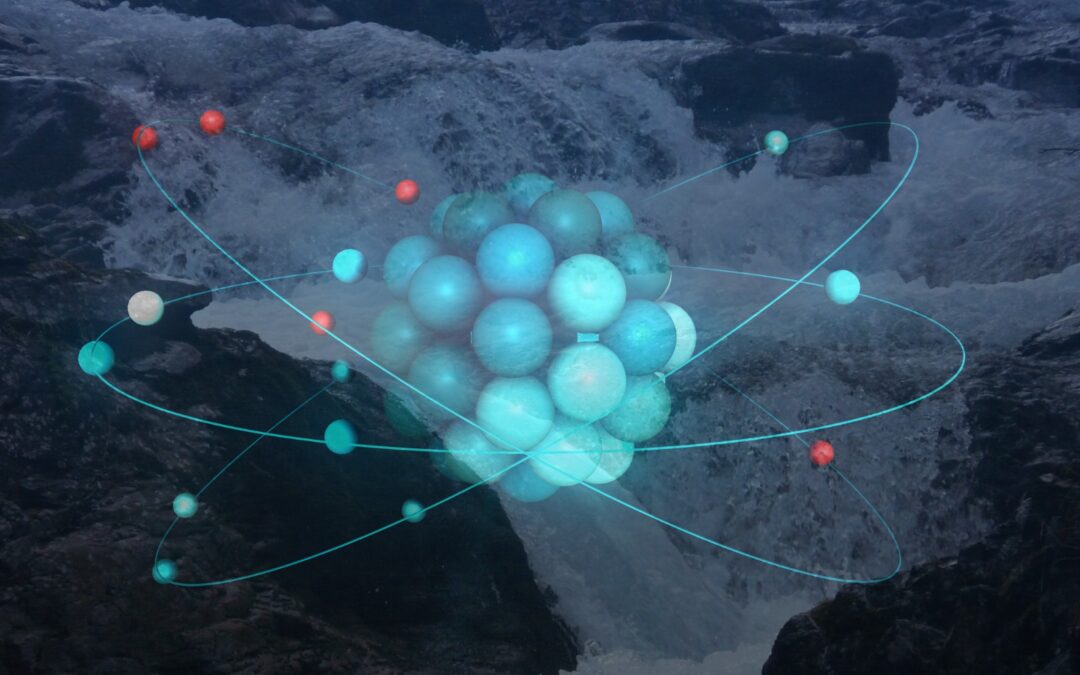
Electron streams of today, pure water streams of tomorrow
Treatment and purification of wastewater from different industries by electrochemical methods
The modern world is inconceivable without the various industries that shape it: the creation of value-added products from raw materials, although a concept as old as civilisation itself, would not have developed so rapidly without the Industrial Revolution, which made it possible to obtain products with little difference between them in less time and at a lower price.
Like everything else, this growth of the industry has brought with it a number of problems. Many of these have been solved over time or have been properly minimised to the point where they are no longer a problem. At the end of the day, the aim is to produce as little waste as possible in the transformation of raw materials into products, as this generation involves the treatment of waste in order to dispose of it properly.
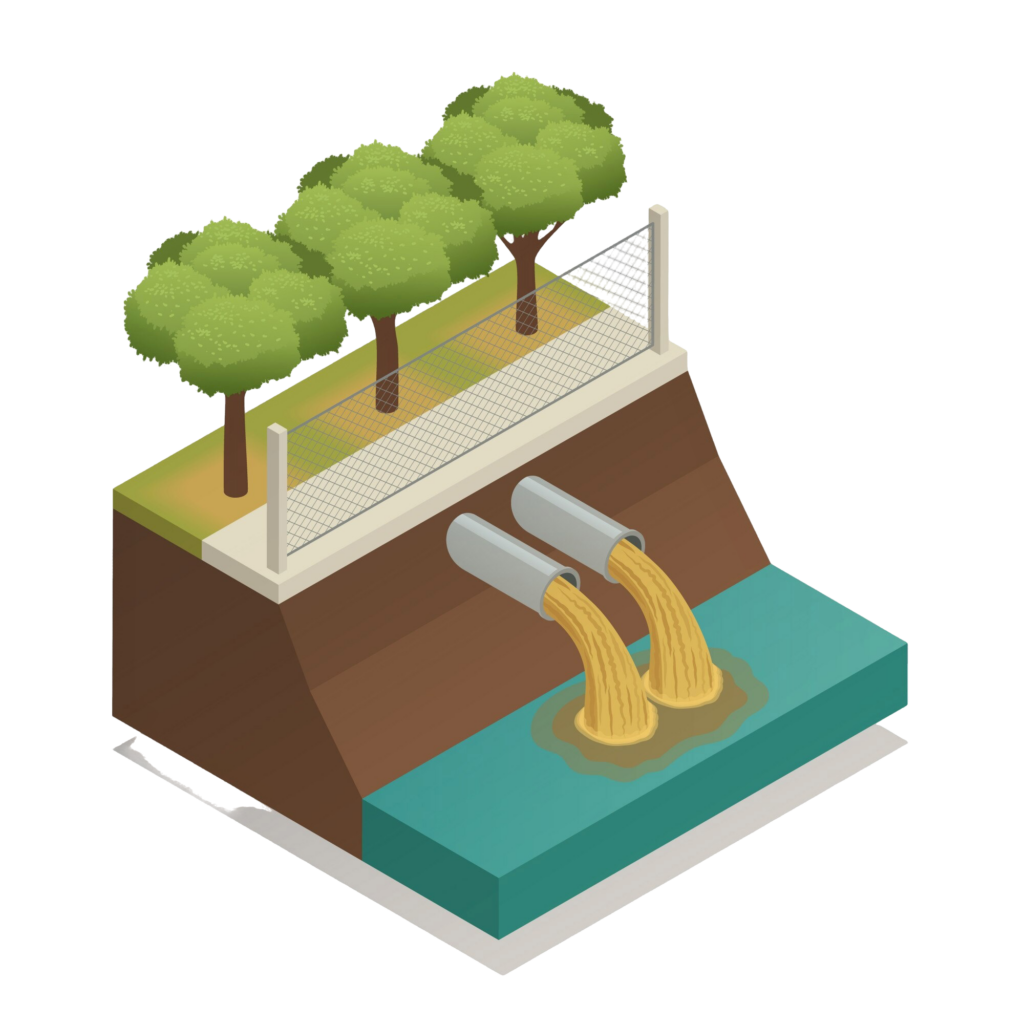
Even so, there are some industries that are known to leave an indelible mark on the area in which they are located, such as the paper industry. It should be added that in the last 20 years the regulations implemented, as well as the work carried out by the pulp treatment companies themselves, has helped to reduce the industry’s carbon footprint (an environmental indicator that aims to reflect the total greenhouse gases emitted as a direct or indirect effect of, in this case, an organisation).
But, even with the work done so far, a system in which the waste generated is zero is impossible. An industry such as the paper industry will always generate wastewater that must be treated differently from that generated in households. Therefore, many companies in the industry are looking for ways to inert their waste flows so that they do not pose a problem for the environment.
Another industry that suffers from the same problem as the paper industry is the mining industry, where the extracted heavy metals are part of the gangue of the ore, which is of no economic interest to the company. The problem is when the concentration of heavy metals is too low to be trapped by physical methods such as coagulation or flocculation. Although the amount of metals in the waste streams is reduced, there is a certain amount of compounds harmful to the environment and humans that give the waste streams a concentration above the recommended levels.
To solve these problems, different techniques have been proposed to control the amount of harmful components that industries can discharge, but, in this blog entry, I want to talk mainly about different electrochemical techniques that exist to carry out this task. To do so, I think it is appropriate to make a brief summary of the branch that uses these techniques, which is electrochemistry.
Electrochemistry overview
Electrochemical reactions can be divided according to the potential needed to carry them out. When chemical reactions are induced by an external potential difference, i.e. a voltage needs to be applied to carry it out, the process is called electrolysis. On the other hand, if the electrical potential difference arises as a result of a chemical reaction, i.e. a voltage is generated as a consequence of the reaction, we are dealing with an ‘electrical energy accumulator’, commonly known as a battery or galvanic cell.
“Electrolysis. When chemical reactions are induced by an external potential difference”
Chemical reactions in which electrons are transferred between molecules are called redox reactions, which comes from the fact that, for a complete electrochemical reaction to take place, there must be a half-reaction in which one compound is reduced and another half-reaction in which another compound is oxidised, thus giving rise to this type of reaction. These reactions are essential in electrochemistry, as they enable the processes that generate or are induced by electricity.
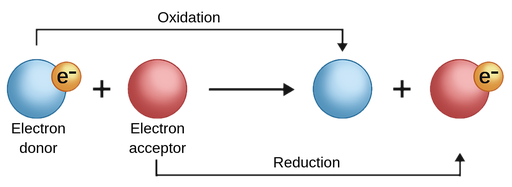
In general terms, electrochemistry is concerned with investigating cases where oxidation and reduction reactions occur separately, either physically or at different times, within a system connected to an electrical circuit. This aspect is studied in analytical chemistry, specifically in potentiometric analysis.
The use of electrochemistry in industrial wastewater is based on the fact that metal ions often have different oxidation states (the theoretical electrical charge that an atom would have if all its bonds with other elements were completely ionic). By playing with these oxidation states and the presence of counterions that are capable of forming a low-solubility salt, a large part of the heavy metals can be removed, as well as other ions that are likely to be harmful.
Paper industry: capacitive deionisation
In the case of CARTIF, one of the electrochemical techniques used to treat effluent water from the paper industry is capacitive deionisation.
Capacitive deionisation (CDI) technology is based on the removal of anions and cations using an electric field and electrodes composed of carbon-derived materials with high porosity and good electrical conductivity. This method allows the localised accumulation of positive and negative charges around the electrodes in an alternating cell process, in which each cell functions as a supercapacitor that stores electrical energy while reducing the conductivity of the solution due to the removal of charges from the medium.
The inversion of polarity makes it possible to recover the accumulated energy at the same time as cleaning the electrodes on the surface of which the ions of opposite charge have been deposited. Thus, by circulating water against the current, a large part of the energy previously used in the desalination process is recovered, which can be reused to continue reducing the amount of dissolved salts. This process is repeated in cycles through several cells connected in parallel, alternating cells in operation and cells in cleaning. This makes it possible to obtain a continuous flow of desalinated water, a rejection flow (current with a high concentration of salts, which, as its concentration increases, is easier to dry and store in the future) and an energy recovery that is used in the active cells.
“Inversion of polarity. Recover the accumulated energy at the same time as cleaning the electrodes on the surface of which the ions of opposite charge have been deposited.”
The main advantages of the CDI are:
- Lower energy consumption compared to reverse osmosis (RO, which is based on applying pressure to the solution to push it through a semi-permeable osmosis membrane to filter it and remove the ions present) as it does not require high pressures to operate and allows recovery of much of the energy used in desalination, stored in the cells as in a capacitor.
- Reduction in the use of chemicals, as no chelating agents are required to prevent clogging as in membrane-based technologies, as well as no need for acids and bases for resin regeneration in ion exchange systems.
- Modularity and compactness. The possibility of using multiple cells in parallel facilitates compact assembly and progressive expansion of the treatment flow by adding modules, offering scalable growth and greater versatility, which is of great interest in the industry.
Mining industry: electrocoagulation
In the case of the mining industry, one technique that CARTIF has been considering is electrocoagulation (EC), which has a range of application that also covers suspended solids, emulsified oil, hydrocarbons and the like.
In its simplest form, an electrocoagulation reactor consists of an electrolytic cell with an anode and a cathode. When connected to an external power source, the anode material corrodes electrochemically due to oxidation, while the cathode undergoes passivation.
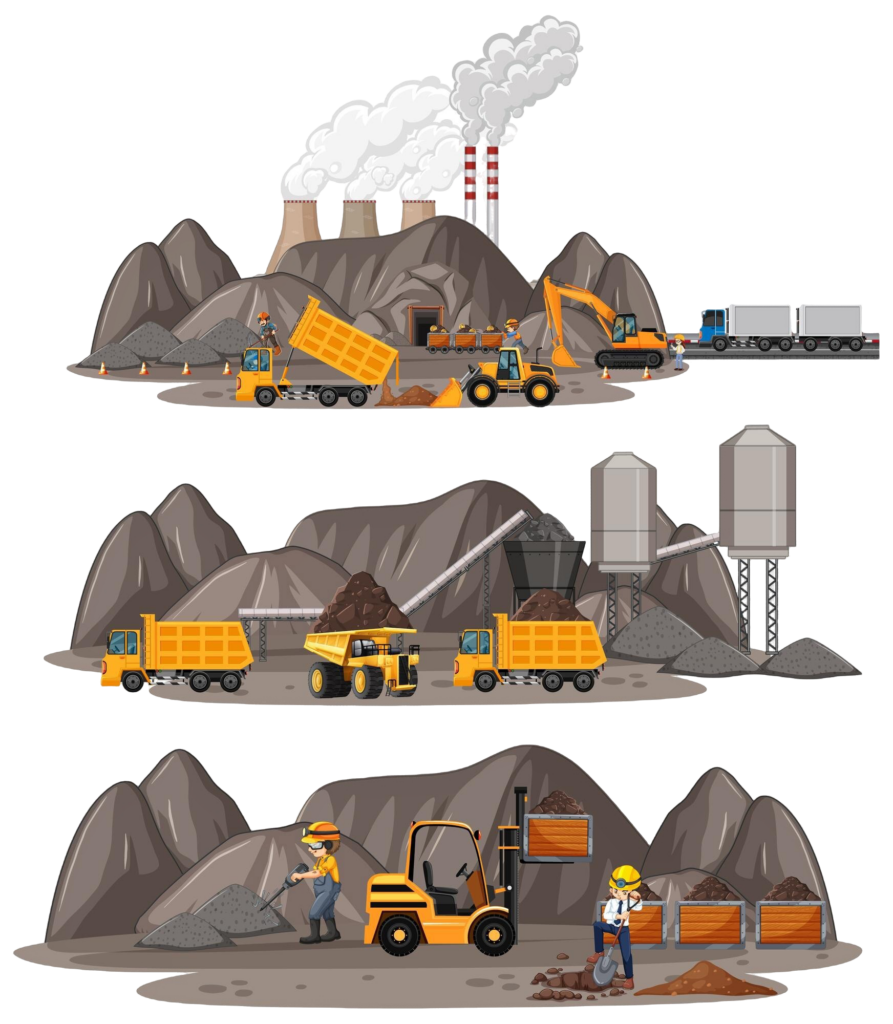
An electrocoagulation (EC) system essentially consists of pairs of conductive metal plates in parallel, which act as monopolar electrodes. In addition, it requires a DC current source, a resistance box to regulate the current density and a multimeter to read the current values. The conductive metal plates are commonly known as ‘sacrificial electrodes’. The sacrificial anode reduces the dissolution potential of the anode and minimises the passivation of the cathode. Sacrificial anodes and cathodes can be made of the same material or of different materials, depending on the composition of the solution to be treated.
The monopolar electrode arrangement with cells in series is electrically similar to a single cell with many electrodes and interconnections. In a series cell arrangement, a higher potential difference is required for a given current to flow, as cells connected in series have higher resistance. However, the same current will flow through all electrodes. In contrast, in a parallel or bipolar arrangement, the electric current is divided between all electrodes relative to the resistance of the individual cells, and each electrode face has a different polarity.
During electrolysis, the positive side undergoes anodic oxidation reactions, while the negative side undergoes cathodic reduction reactions. Consumable metal plates, such as iron or aluminium, are generally used as sacrificial electrodes to continuously produce ions in the water. The released ions neutralise the charges of the particles present in the solution and initiate coagulation. These ions remove undesirable contaminants, either by chemical reaction and precipitation, or by causing coalescence of colloidal materials, which can then be removed by removal of the organic layer that forms on the surface of the solution. In addition, as water containing colloidal particles, oils or other contaminants moves through the applied electric field, ionisation, electrolysis, hydrolysis and free radical formation can occur, which can alter the physical and chemical properties of the water and contaminants. As a result, the reactive and excited state causes the contaminants to be released from the water and destroyed or made less soluble.
Some of the advantages of this system, in comparison with the chemistry coagulation, are:
- The flocs formed by EC are similar to flocs generated by chemical flocculation, except that EC flocs tend to be much larger, contain less bound water, are acid resistant and more stable, and can therefore be separated more quickly by filtration.
- EC can produce an effluent with lower total dissolved solids (TDS) content compared to chemical treatments, particularly if metal ions can precipitate as insoluble hydroxides or carbonates.
- The EC process has the advantage of removing smaller colloidal particles, as the applied electric field neutralises any residual charge, thus facilitating coagulation through the formation of larger micelles.
- The CE process generally avoids the excessive use of chemicals, which reduces the need to neutralise excess products and reduces the possibility of secondary contamination caused by chemicals added in high concentration, as is the case when chemical coagulation is used in wastewater treatment.
- The gas bubbles produced during the electrolysis of both the water in the solution and the components in the solution can conveniently transport the contaminating components to the surface of the solution, where they can be more easily concentrated, collected and removed.
In conclusion, we can state that industrial evolution has brought with it significant environmental challenges, especially in the management of waste and toxic pollutants. To mitigate these effects, electrochemistry has emerged as a key tool in wastewater purification, highlighting techniques such as capacitive deionisation (CDI) and electrocoagulation (EC). These technologies make it possible to reduce the concentration of heavy metals and other pollutants with less use of chemicals and lower energy consumption. Thus, electrochemistry offers sustainable solutions to minimise the ecological impact of industries by optimising the treatment of their waste and contributing to environmental protection.